Fotos: HSM Stahl- und Metallhandel GmbH
Rippenrohre kommen in zahlreichen Industrien und Anwendungen zum Einsatz. In der Energieerzeugung spielen sie in Kraftwerken eine zentrale Rolle bei der effizienten Wärmetauschung. In Raffinerien und der Petrochemie dienen sie der Kühlung und Erwärmung von Flüssigkeiten und Gasen. In Industrieanlagen der Chemieindustrie sind sie für komplexe Produktionsprozesse mit hohen thermischen Anforderungen unverzichtbar. Heizungs- und Kühlsysteme nutzen Rippenrohre zur Temperierung von Gebäuden und Produktionsstätten, während sie in Haushaltsgeräten wie Klimaanlagen oder Wärmepumpen ebenfalls eine wichtige Funktion übernehmen. Durch ihre vergrößerte Oberfläche tragen Rippenrohre entscheidend zur Verbesserung der Wärmeübertragungseffizienz bei. Ihre Vielseitigkeit macht sie zu einer bevorzugten Lösung in zahlreichen thermischen Anwendungen.
Ein Gastbeitrag von Wilfried Schöner, Projektmanagement bei HSM Stahl- und Metallhandel GmbH

Bedeutung von Rippenrohren in der Industrie
Rippenrohre spielen eine essenzielle Rolle in der Raffinerie-, Petrochemie- und Chemieindustrie, insbesondere in Wärmetauscher-Systemen wie Luftkühlern. Diese speziellen Rohre ermöglichen eine effiziente Kühlung und tragen zur Temperaturregulierung von Flüssigkeiten und Gasen bei. Eine optimierte Wärmeübertragung durch Rippenrohre ist entscheidend, um Betriebskosten zu senken, die Sicherheit zu erhöhen und die Effizienz von Wärmetauschern erheblich zu steigern.
Auch im Bereich des Erdgastransports sind Rippenrohre unverzichtbar. Da ein Transport über Pipelines nicht immer möglich ist, muss Erdgas durch Abkühlung verflüssigt werden. Hier kommen Hochleistungsrippenrohre in Rohrbündelwärmeaustauschern zum Einsatz, die sowohl innen als auch außen berippt sind.
Diese Bauweise maximiert die Wärmeübertragung und sorgt für eine effiziente Verflüssigung des Gases.
Materialien von Rippenrohren
Rippenrohre bestehen aus einem Kernrohr und den Rippen auf dem Rohr. Je nach Einsatzgebiet kann sowohl für das Kernrohr, als auch für die Rippen das passende Material verwendet werden. Gängige Materialien für das Kernrohr sind neben Edelstahl auch NE-Metalle oder Stahl. Für die Rippen wird Kupfer, Aluminium und verzinkter Stahl verwendet.
Das am häufigsten eingesetzte Material für Rippenrohre ist Edelstahl, aufgrund seiner hohen Korrosionsbeständigkeit und Langlebigkeit. Dies ist in Umgebungen mit aggressiven Medien oder extremen Temperaturen bis zu 1.000 Grad von großer Bedeutung. Edelstahl bietet den Vorteil einer hohen mechanischen Stabilität und Beständigkeit gegen thermische Belastungen, wodurch er sich ideal für anspruchsvolle Industrieanwendungen eignet.
Die Rippen werden meistens aus Reinalluminium gefertigt, das eine gute Leitfähigkeit, hohe Korrosionsbeständigkeit, hohe Festigkeit und ein leichtes Gewicht aufweist.
Das Unternehmen HSM® hat umfassende Erfahrung in der Beschaffung, dem Transport und der Abnahme von Edelstahl-Rippenrohren. Besonders bei Nischenprodukten für spezielle Anforderungen kann HSM® auf ein tiefgehendes Fachwissen zurückgreifen.
Für die verschiedenen Arten von Rippenrohren und ihre spezifischen Einsatzbereiche bieten die Experten maßgeschneiderte Lösungen.
Arten der Berippung und Anwendungen
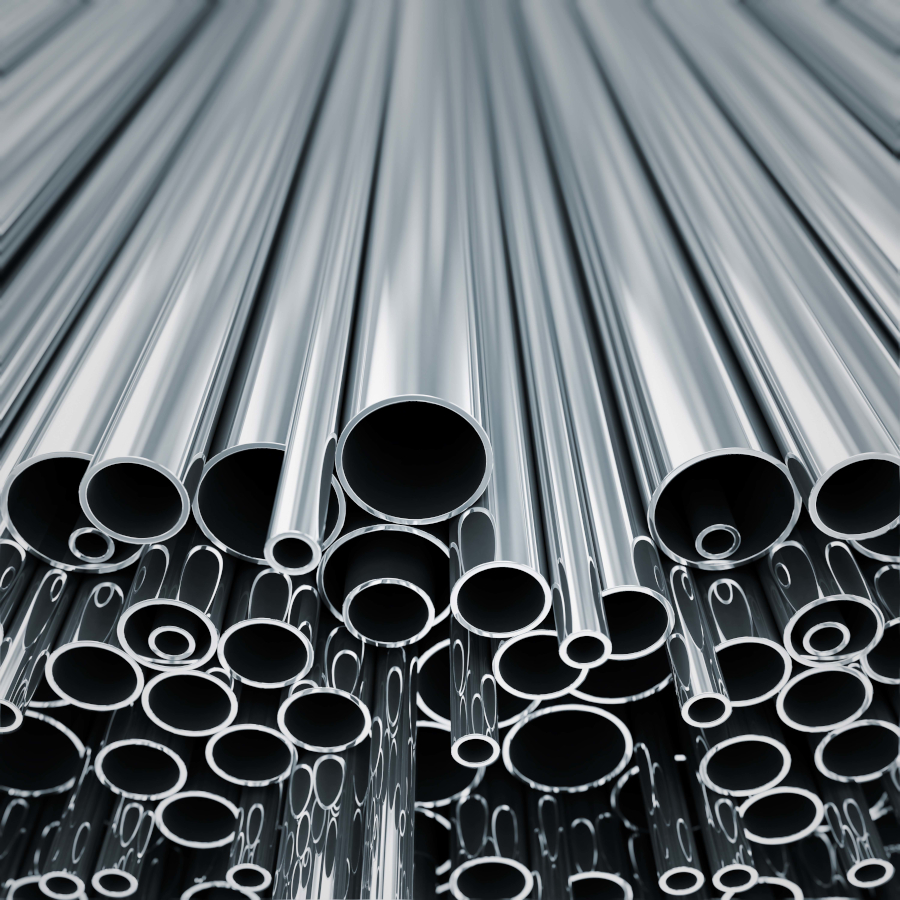
Rippenrohre gibt es in unterschiedlichen Ausführungen, was Form und Verarbeitung angeht. Diese Ausprägungen haben verschiedene Vor- und Nachteile, vor allem in Bezug auf Wärmeaustausch, Korrosionsbeständigkeit und Langlebigkeit:
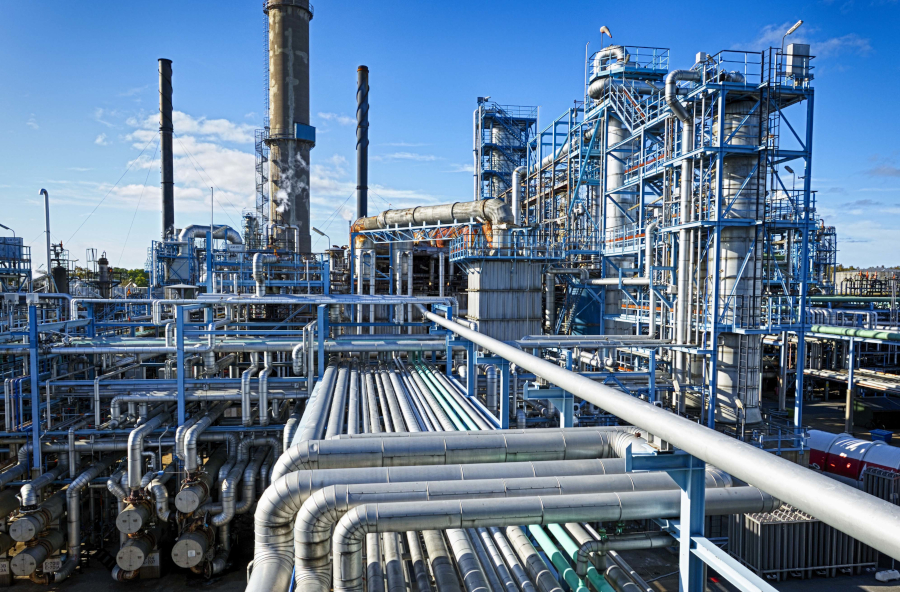
Lamellenrippenrohre verbessern den Wärmeaustausch durch eine vergrößerte Oberfläche, während Noppen-Rippenrohre (bestiftete Rohre) für extrem korrosive Umgebungen geeignet sind.
Nicht verlötete Rippenrohre, auch als gewickelte oder gewalzte Rippen bekannt, bieten eine kostengünstigere Wärmeübertragung bei geringer Belastung. Die Nachteile dabei sind Einbußen in der Wärmeübertragung, da die Rippen mit dem Kernrohr nicht so fest verbunden sind, Instabilität, Korrosionsanfälligkeit und damit verbundene höhere Wartungskosten. Dafür haben sie eine höhere Flexibilität und kein Risiko für Lötfehler.
Verlötete Rippenrohre zeichnen sich durch eine höchst effiziente Wärmeübertragung bei hoher Belastbarkeit aus.
Der Korrosionsschutz und die mechanische Stabilität wird an den Lötstellen noch erhöht und der Wärmewiderstand minimiert. Dafür sind sie kostenintensiver und komplexer in der Herstellung.
Extrudierte Rippen sind qualitativ sehr hochwertig. Sie bieten eine besondere Langlebigkeit und Widerstandsfähigkeit, sie sind sozusagen die Könige unter den Rippenrohren, allerdings auch mit höheren Kosten verbunden.
Herstellung von Rippenrohren
Die Herstellung von Rippenrohren erfolgt in mehreren Schritten und variiert je nach Art des Rippenrohrs sowie den spezifischen Anforderungen. Zunächst wird das geeignete Material für das Innenrohr und die Rippen ausgewählt. Anschließend wird das Innenrohr meistens auf die gewünschte Länge geschnitten und gegebenenfalls vorbehandelt, um eine optimale Verbindung mit den Rippen zu gewährleisten. Beim Aufbringen der Rippen kommen unterschiedliche Verfahren zum Einsatz.
Nicht verlötete Rippenrohre werden gewickelt oder gewalzt. Beim Wickelverfahren wird das Rippenmaterial spiralförmig um das Innenrohr gewickelt, wobei das Rippenband unter Spannung gehalten wird, um eine stabile Verbindung sicherzustellen. Das Walzverfahren nutzt spezielle Walzenmaschinen, die das Rippenmaterial um das Innenrohr formen und fest anpressen. In einigen Fällen erfolgt die Fixierung der Rippen zusätzlich durch mechanische Verformung, um eine dauerhafte Verbindung zu garantieren.
Verlötete Rippenrohre werden unterteilt in Spiralrippenrohre und segmentierte Rippenrohre. Bei Spiralrippenrohren wird ein Metallband spiralförmig um das Innenrohr gewickelt und kontinuierlich verschweißt, was durch Hochfrequenzschweißen oder Widerstandsschweißen erfolgt. Bei segmentierten Rippenrohren wird das Rippenband in kurze Abschnitte unterteilt und in regelmäßigen Abständen auf das Innenrohr geschweißt.
Extrudierte Rippen werden durch Querwalzen (Extrusion) aus einer auf das Kernrohr aufgeschobenen Aluminium-Luppe erzeugt. Dieses Verfahren sorgt für eine ausgezeichnete Verbindung zwischen dem Kernrohr und der Rippe. Zudem wird das Kernrohr vollständig mit Aluminium ummantelt, was einen hervorragenden Korrosionsschutz bietet.
Qualitätsprüfung und Abnahmeverfahren
Die Qualitätssicherung spielt eine zentrale Rolle bei der Herstellung und Lieferung von Rippenrohren für industrielle Anwendungen. HSM® hat beispielsweise bei der Zusammenarbeit mit einer Raffinerie eine nach Zeichnungsvorgabe erstellte Rippenrohrlösung mit extrudierten Rippen geliefert, die dem Widerstand im Außenbereich standhalten. Dabei wurden umfangreiche Qualitätsprüfungen durchgeführt, um sicherzustellen, dass die mechanische Belastbarkeit und die Wärmeübertragungseffizienz den hohen Anforderungen entsprechen. Die standardmäßigen Prüfverfahren umfassen die visuelle Inspektion auf sichtbare Mängel, die Maßkontrolle zur Überprüfung der Einhaltung der

Toleranzen sowie die Druckprüfung zur Sicherstellung der Dichtigkeit und Festigkeit durch ein Prüfmedium wie Wasser oder Luft. Hierbei wird Druck aufgebaut, konstant gehalten und auf Leckagen überwacht. Zusätzlich erfolgt ein Druckabfalltest. Eine Ultraschallprüfung erkennt interne Materialfehler, während eine Röntgenprüfung die innere Struktur der Rohre analysiert.
Relevante Normen und Vorschriften
Die Einhaltung internationaler Standards ist für die Qualitätssicherung von Rippenrohren unerlässlich. Zu den wichtigsten Normen gehören die DIN EN 10217-7, die Anforderungen an geschweißte Stahlrohre für Druckbeanspruchungen festlegt, das AD 2000 Regelwerk in Kombination mit VdTÜV-Merkblättern, ein anerkanntes technisches Regelwerk für Druckgeräte in Deutschland basierend auf der europäischen Druckgeräterichtlinie (DGRL 2014/68/EU) und der ASME Boiler and Pressure Vessel Code (BPVC), der Vorschriften für Druckbehälter und Wärmetauscher definiert, die Anforderungen an Qualitätsmanagementsysteme stellt. Für HSM® ist hohe Qualität keine Besonderheit, sondern eine Selbstverständlichkeit. Die konsequente Einhaltung dieser Normen gewährleistet sichere und langlebige Lösungen für industrielle Anwendungen.
Über den Artikel der Woche
Jede Woche beleuchten wir im Artikel der Woche ein spannendes Thema für die Edelstahlbranche. Weitere Artikel finden Sie auch in unserer Zeitschrift Edelstahl Aktuell. Um diese und viele weitere Artikel (fast) monatlich zu lesen, abonnieren Sie unsere Zeitschrift (erhältlich in Print und digital).
Möchten Sie als Autor mitwirken? Bitte kontaktieren Sie Sonja Wingels.
Jede Woche teilen wir einen neuen Artikel mit unserer Edelstahl Community. Machen Sie mit und lassen Sie uns Ihren Artikel auf Edelstahl Aktuell online und in gedruckter Form veröffentlichen.