Foto: Airbus Space and Defence SAS
AddUp, ein globaler OEM für die additive Fertigung von Metall, und Airbus Defence & Space haben den ersten Metall-3D-Drucker an die Europäische Weltraumorganisation geliefert. Dieser Metall-3D-Drucker wurde von einem industriellen Team unter der Leitung von Airbus Defence and Space im Rahmen eines Vertrags mit der Europäischen Weltraumorganisation (ESA) entwickelt, der von Airbus Defence and Space mitfinanziert wurde.
Der Metall-3D-Drucker wurde laut Pressemeldung von AddUp entwickelt, um die Fähigkeiten und die Leistung der additiven Technologie zu bewerten und die Metallabscheidung in 3D unter anhaltenden Mikrogravitationsbedingungen durchzuführen. Der Metall-3D-Drucker sei am Dienstag, dem 30. Januar 2024, im Rahmen der Mission NG-20 erfolgreich an Bord der Internationalen Raumstation gestartet. Der Druckbetrieb werde voraussichtlich Ende Februar oder Anfang März beginnen. Nach der Installation durch ESA-Astronaut Andreas Morgensen wird der Drucker laut ESA von der Erde aus gesteuert und überwacht, so dass der Druckvorgang ohne Morgensens Aufsicht stattfinden kann.
3D-Druck aus Metall macht Astronauten das Leben leichter
An Bord der Internationalen Raumstation (ISS) befinden sich laut Presseinformation bereits mehrere Kunststoff-3D-Drucker, von denen der erste 2014 angekommen ist. Die Astronauten hätten sie bereits genutzt, um Kunststoffteile zu ersetzen oder zu reparieren, denn eines der größten Probleme des Alltags im Weltraum ist die Versorgung mit Ausrüstung, die manchmal Monate auf sich warten lässt. Aber nicht alles kann aus Kunststoff hergestellt werden.
Dieser logistische Engpass werde sich auf zukünftigen Mond- und Marsstationen in den nächsten Jahrzehnten noch verschärfen. Auch wenn das Rohmaterial noch auf den Weg gebracht werden müsse, sei das Drucken des Teils immer noch effizienter als der Transport des gesamten Teils bis zu seinem Bestimmungsort.
„Der 3D-Metalldrucker wird neue Fertigungsmöglichkeiten in der Umlaufbahn bieten, einschließlich der Möglichkeit, tragende Strukturteile herzustellen, die widerstandsfähiger sind als ein entsprechendes Kunststoffteil. Die Astronauten werden in der Lage sein, Werkzeuge wie Schraubenschlüssel oder Montageschnittstellen, die mehrere Teile miteinander verbinden können, direkt herzustellen. Die Flexibilität und schnelle Verfügbarkeit des 3D-Drucks wird die Autonomie der Astronauten erheblich verbessern“, so Gwenaëlle Aridon, leitende Ingenieurin bei Airbus Space Assembly.
Die Herausforderungen des Metalldrucks im Weltraum
Während das Verfahren des 3D-Drucks auf der Erde beherrscht wird, stelle der Druck von Metall im Weltraum eine Reihe eigener technischer Herausforderungen dar. Sébastien Girault, Systemingenieur für Metall-3D-Drucker bei Airbus, erklärt. „Die erste Herausforderung bei diesem Technologiedemonstrator war die Größe. Auf der Erde werden die derzeitigen Metall-3D-Drucker in einem mindestens zehn Quadratmeter großen Labor installiert. Um den Prototyp für die ISS herzustellen, mussten wir den Drucker auf die Größe einer Waschmaschine verkleinern.“ Diese Verkleinerung sei notwendig, damit der Drucker in das Gestell passt, in dem er an Bord des Columbus-Labors der ISS untergebracht sein wird. „Bei dieser Größe können wir Teile mit einem Volumen von neun Zentimetern Höhe und fünf Zentimetern Breite drucken“, so Girault.
Die zweite Herausforderung sei die Sicherheit: der Schutz der ISS vor der aggressiven Druckumgebung, die durch den Laser und die von ihm erzeugte Hitze entsteht. Der Drucker befinde sich in einer abgedichteten Metallbox, die wie ein Safe wirkt. Der Schmelzpunkt von Metalllegierungen, die mit diesem Verfahren kompatibel sind, kann laut Airbus weit über 1.200 °C liegen, während er bei Kunststoffen bei etwa 200 °C liegt, was eine drastische Wärmekontrolle erfordert.
„Die Beherrschung der Schwerkraft ist ebenfalls von entscheidender Bedeutung, weshalb wir uns für die drahtbasierte Drucktechnologie entschieden haben. Der Draht ist unabhängig von der Schwerkraft, im Gegensatz zum pulverbasierten System, das immer auf den Boden fallen muss”, so Girault.
Unabhängig davon, ob es sich um Kunststoff oder Metall handelt, werden Dämpfe freigesetzt, die mit Filtern behandelt und in der Maschine aufgefangen werden müssen, damit sie die Luft in der ISS nicht verunreinigen. „Sicherheit und Kontamination sind für uns nicht nur für die ISS, sondern auch für den künftigen Einsatz auf dem Mond von entscheidender Bedeutung”, so Gwenaëlle Aridon.
Der Drucker wird mit einer Art von rostfreiem Stahl drucken, der wegen seiner guten Korrosionsbeständigkeit häufig für medizinische Implantate und zur Wasseraufbereitung verwendet wird, heißt es in einer Meldung von ESA. Der Edelstahldraht werde in den Druckbereich eingeführt, der durch einen Hochleistungslaser erhitzt wird, der etwa eine Million Mal stärker sei als ein durchschnittlicher Laserpointer. Beim Eintauchen des Drahtes in das Schmelzbad schmelze das Drahtende, und das Metall werde dem Druck hinzugefügt.
„Das Schmelzbad des Druckverfahrens ist sehr klein, in der Größenordnung eines Millimeters, so dass die Oberflächenspannung des flüssigen Metalls es in der Schwerelosigkeit sicher an seinem Platz hält. Allerdings liegt der Schmelzpunkt von rostfreiem Stahl bei etwa 1400 °C, so dass der Drucker in einer vollständig abgedichteten Box arbeitet, die verhindert, dass überschüssige Hitze oder Dämpfe die Besatzung der Raumstation erreichen.
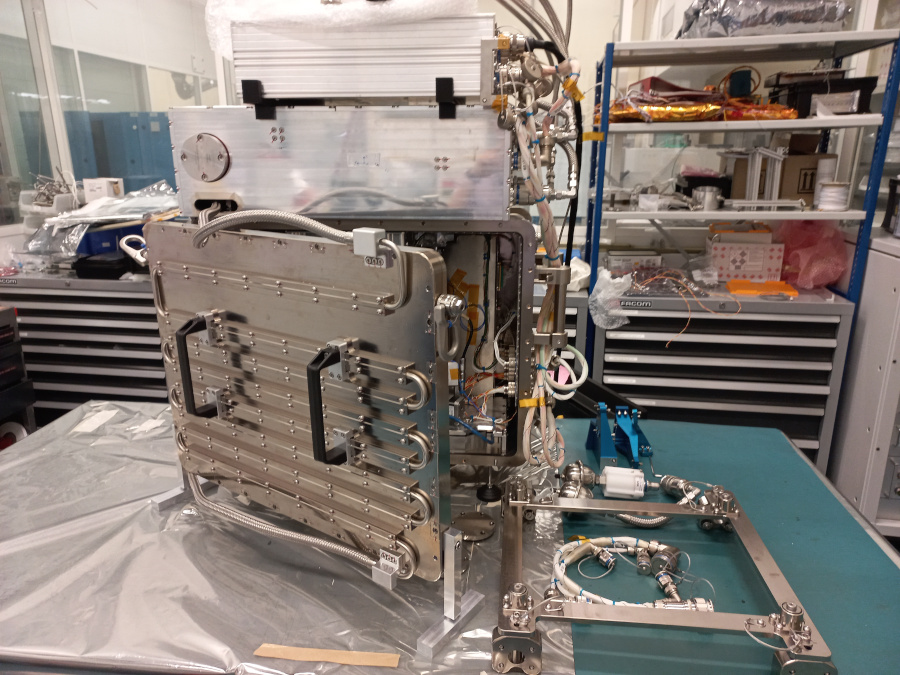
Und bevor der Druckvorgang beginnt, muss die interne Sauerstoffatmosphäre des Druckers in den Weltraum entlüftet und durch Stickstoff ersetzt werden – der heiße Edelstahl würde oxidieren, wenn er dem Sauerstoff ausgesetzt wäre“, so ESA-Materialingenieur Advenit Makaya vom ESA-Direktorat für Technologie, Engineering und Qualität, der technische Unterstützung für das Projekt leistete.
Eignet sich der Metalldruck für eine Umgebung unter Schwerelosigkeit?
Dies ist eine der Fragen, die das Team beantworten will. Für dieses Experiment werden laut Aussage von Airbus zwei Drucker verwendet: das „Flugmodell” in der ISS und das „Ingenieursmodell” auf der Erde. Es wurden vier Formen ausgewählt, um die Leistung des Metall-3D-Druckers zu testen. Diese ersten Objekte werden mit denselben Formen verglichen, die auf dem Boden gedruckt wurden, den sogenannten Referenzdrucken, um zu sehen, wie die Weltraumumgebung den Druckprozess beeinflusst. Die vier Drucke sind laut Information von ESA alle kleiner als eine Getränkedose, wiegen weniger als 250 g pro Druck und benötigen etwa zwei bis vier Wochen zum Drucken. Die geplante Druckzeit sei aufgrund der Lärmvorschriften auf der Raumstation auf vier Stunden täglich begrenzt – die Ventilatoren und der Motor des Druckers seien relativ laut.
Ein Referenz- und 0xg-Druck, der Teil eines speziellen Werkzeugs ist, werde an das Europäische Astronautenzentrum (EAC) in Köln, Deutschland, geschickt. Zwei weitere werden an das technische Herz der ESA, das Europäische Weltraumforschungs- und Technologiezentrum (ESTEC) übergeben, wo ein Team des Labors für Werkstoffe und elektrische Komponenten die Proben für die Makro- und Mikroanalyse der gedruckten Teile erwarte. Der letzte Druck gehe an die Technische Universität Dänemark (DTU), die seine Form vorgeschlagen hat und seine thermischen Eigenschaften untersuchen werde, um z. B. die zukünftige Ausrichtung der Antenne zu unterstützen.
Vorbereitungen für die Zukunft
Der 3D-Metalldruck an Bord der ISS werde dazu beitragen, die Qualität des Metalldrucks in der Umlaufbahn besser zu verstehen, und wertvolle Erkenntnisse über den Betrieb eines 3D-Metalldruckers im Weltraum liefern. Der Druck von Strukturteilen im Weltraum ist laut Airbus ein wichtiger Schritt bei der Vorbereitung der Technologien, die die Menschheit für eine dauerhafte Präsenz auf dem Mond benötigt.
„Die Erhöhung des Entwicklungs- und Automatisierungsgrads der additiven Fertigung im Weltraum könnte einen Wendepunkt für die Unterstützung des Lebens jenseits der Erde darstellen”, betont Aridon. „Wenn man über die ISS hinausdenkt, könnten die Anwendungen erstaunlich sein. Stellen Sie sich einen Metalldrucker vor, der umgewandeltes Regolith (Mondstaub) oder recycelte Materialien zum Bau einer Mondbasis verwendet!”
Eines der Ziele der ESA für die künftige Entwicklung ist die Schaffung einer Kreislaufwirtschaft im Weltraum und die Wiederverwertung von Materialien in der Umlaufbahn, um eine bessere Nutzung der Ressourcen zu ermöglichen. Eine Möglichkeit wäre die Wiederverwendung von Teilen aus alten Satelliten für neue Werkzeuge oder Strukturen. Der 3D-Drucker würde es überflüssig machen, ein Werkzeug mit einer Rakete hochzuschicken, und es den Astronauten ermöglichen, die benötigten Teile im Orbit zu drucken.
Tommaso Ghidini, Leiter der Abteilung für Mechanik bei der ESA, stellt fest: „Der 3D-Metalldruck im Weltraum ist eine vielversprechende Möglichkeit zur Unterstützung künftiger Explorationsaktivitäten, aber auch darüber hinaus, um zu nachhaltigeren Weltraumaktivitäten beizutragen, durch In-situ-Fertigung, Reparatur und möglicherweise Recycling von Weltraumstrukturen für eine breite Palette von Anwendungen. Dazu gehören die Herstellung und Montage großer Infrastrukturen in der Umlaufbahn sowie die langfristige Besiedlung des Planeten durch Menschen. Diese Aspekte stehen im Mittelpunkt der bevorstehenden technologieübergreifenden Initiativen der ESA”.
Thomas Rohr, Leiter der ESA-Sektion Materialien und Prozesse, fügt hinzu: „Diese Technologiedemonstration, die die Verarbeitung von metallischen Werkstoffen in der Mikrogravitation zeigt, ebnet den Weg für künftige Bestrebungen zur Herstellung von Infrastrukturen außerhalb der Erde.”
—
Der 3D-Metalldrucker wurde von einem Konsortium aus Airbus Defence and Space, AddUp, der Universität Cranfield und Highftech Engineering im Rahmen eines von der Europäischen Weltraumorganisation (ESA) finanzierten Programms entwickelt. Die hier geäußerten Meinungen aus Pressemeldungen von Airbus Defence and Space sowie AddUp können in keiner Weise als die offizielle Meinung der ESA angesehen werden.
Über den Artikel der Woche
Jede Woche beleuchten wir im Artikel der Woche ein spannendes Thema für die Edelstahlbranche. Weitere Artikel finden Sie auch in unserer Zeitschrift Edelstahl Aktuell. Um diese und viele weitere Artikel (fast) monatlich zu lesen, abonnieren Sie unsere Zeitschrift (erhältlich in Print und digital).
Möchten Sie als Autor mitwirken? Bitte kontaktieren Sie Catrin Senger.
Jede Woche teilen wir einen neuen Artikel mit unserer Edelstahl Community. Machen Sie mit und lassen Sie uns Ihren Artikel auf Edelstahl Aktuell online und in gedruckter Form veröffentlichen.