Während die Welt nach Klimaneutralität strebt, stellt die CO2-Abscheidung, -Nutzung und
-Speicherung eine wichtige Brücke in eine nachhaltige Zukunft dar. Durch die Abscheidung von CO2 aus industriellen Prozessen wird verhindert, dass schädliche Emissionen in die Atmosphäre gelangen. Die Zuverlässigkeit und Beständigkeit dieser Technologie hängen von molybdänhaltigen Werkstoffen ab.
Ein Gastbeitrag von Dr. Iris Rommerskirchen und Dr. Nicole Kinsman, IMOA
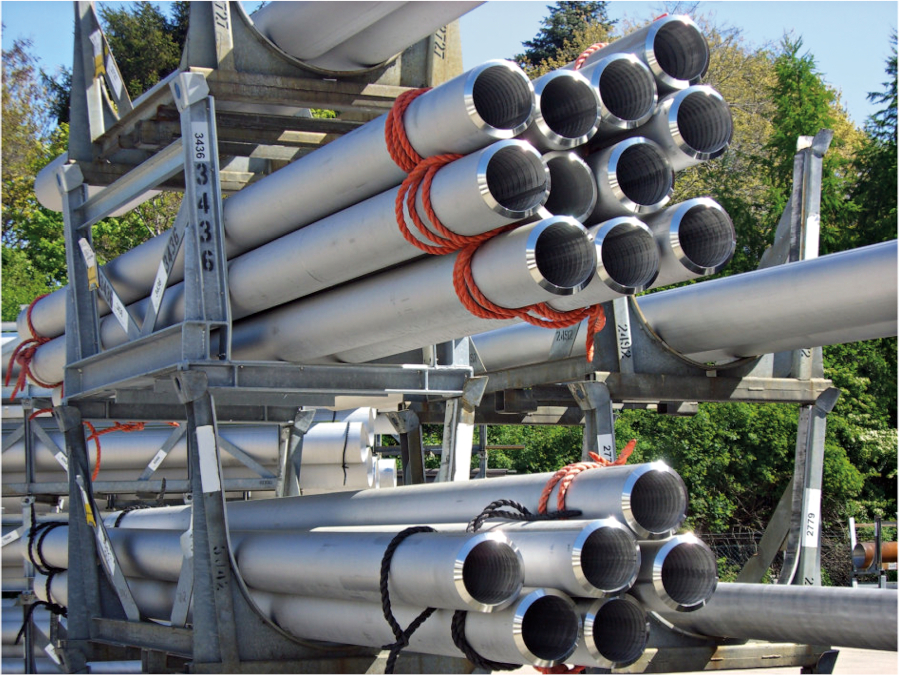
Die Bewältigung der Klimakrise und das Erreichen von Netto-Null-Emissionen bis 2050 gehören zu den größten Herausforderungen unserer Zeit. Der Ausbau erneuerbarer Energien, die Steigerung der Energieeffizienz und die Entwicklung CO2-neutraler Technologien sind entscheidende Schritte in diese Richtung. In der Übergangsphase hin zu einer klimaneutralen Wirtschaft hat sich Carbon Capture, Utilization and Storage (CCUS) als wichtige Strategie zur Erfassung von CO2-Emissionen an ihrer Entstehungsquelle etabliert.
Bei der CCUS-Technologie wird CO2 aus den Abgasen von Industrie- oder Energieerzeugungsanlagen abgeschieden und zur Speicherung oder Wiederverwendung abtransportiert. Das CO2 wird entweder sicher unterirdisch gelagert – bekannt als Carbon Capture and Storage (CCS) – oder für industrielle Anwendungen wie der Herstellung von Chemikalien, synthetischen Kraftstoffen oder
Baumaterialien wiederverwendet. Dieser doppelte Ansatz reduziert nicht nur die Emissionen direkt an der Quelle, sondern verringert auch die Notwendigkeit, neue fossile Brennstoffe zu gewinnen. Die Emissionen in nachgelagerten Prozessen werden dadurch weiter gesenkt. Der Erfolg von CCUS hängt jedoch stark von der Qualität und Sicherheit der Infrastruktur ab – und hier spielt Molybdän eine entscheidende Rolle.
Hürden der Dekarbonisierung
Die vollständige Dekarbonisierung zu erreichen, bleibt nach wie vor ein schwieriges Unterfangen. Steigende Lebensstandards und die zunehmende Digitalisierung führen dazu, dass der weltweite Energiebedarf trotz der Notwendigkeit, Emissionen zu senken, weiter wächst. Kohlenstoff- und energieintensive Branchen wie die Stahlproduktion prüfen bereits neue Lösungen, wie den Ersatz von Koks durch Wasserstoff, der aus erneuerbaren Energien gewonnen wird. Zwar laufen erste Pilotprojekte, doch es wird voraussichtlich noch Jahre dauern, bis solche Verfahren weltweit zum Standard werden.
Auch andere Industriezweige – wie die Glasherstellung, die Ethanolproduktion, die Stromerzeugung, die Synthese von Wasserstoff und Ammoniak, die Düngemittelproduktion, die Erdgasaufbereitung sowie petrochemische Prozesse – stoßen weiterhin CO2 aus und müssen sich verstärkt um die Reduzierung ihrer Emissionen bemühen.
Bei bestimmten chemischen Prozessen sind CO2-Emissionen jedoch unvermeidbar, etwa bei in der Zementherstellung. Hier wird Kalkstein in koksbefeuerten Öfen auf 1500°C erhitzt. Zwar trägt die Verbrennung von Koks zu den Emissionen bei, doch der Großteil – etwa zwei Drittel – stammt aus der chemischen Freisetzung CO2 von im Kalkstein während der Kalzinierung.
Herausforderungen beim Umgang mit CO2
Während reines, trockenes CO2 nicht korrosiv ist, enthält das in CCUS-Systemen abgeschiedene CO2 oft Verunreinigungen wie Wasser, Sauerstoff und Schwefelverbindungen. Bei der Verflüssigung kondensieren diese Stoffe zu aggressiven Säuren, darunter Schwefel-, Salpeter-, Kohlen- und Salzsäure, welche Rohrleitungen, Lagereinrichtungen und andere CCUS-Komponenten erheblich schädigen können.
Neben der Korrosion stellt auch ein plötzlicher Druckabfall in der Flüssigkeit ein Risiko dar. Durch Ausdehnung kühlt das flüssige CO2 schlagartig auf Temperaturen von bis zu -80°C ab – ein Effekt, der als Joule-Thomson-Effekt bekannt ist.
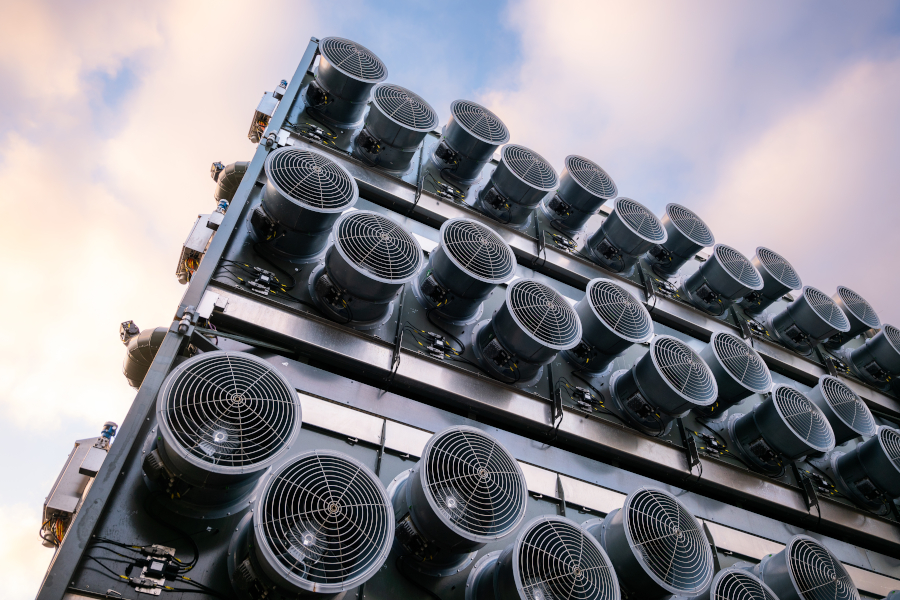
Diese rasche Abkühlung birgt die Gefahr eines Sprödbruchs, eines plötzlichen katastrophalen Versagens von Werkstoffen, deren Zähigkeit bei niedrigen Temperaturen stark abnimmt. Auch die Minustemperaturen, die für den Transport von flüssigem CO2 erforderlich sind, machen Sprödbrüche zu einem ernstzunehmenden Risiko.
Um diesen Herausforderungen zu begegnen, kommen Werkstoffe zum Einsatz, die keinen Übergang von duktil zu spröde aufweisen. Dazu zählen austenitische und super-austenitische nichtrostende Stähle sowie Nickelbasislegierungen. Sie bieten sowohl die erforderliche Zähigkeit bei niedrigen Temperaturen als auch eine hohe Korrosionsbeständigkeit. Duplex- und Super-Duplex-Edelstähle zeichnen sich durch ihre hervorragende Korrosionsbeständigkeit aus und wurden bereits erfolgreich für CO2-Injektionsbohrungen eingesetzt. Zwar zeigen diese bei Minustemperaturen einen Übergang von duktil zu spröde, eignen sich jedoch aufgrund ihrer sehr hohen Festigkeit für den Einsatz unter den gegebenen Umweltbedingungen.
CO2-Abscheidung
Bei der CO2-Abscheidung wird Kohlendioxid aus industriellen Emissionen isoliert – meist durch chemische Absorption oder ähnliche Verfahren. PCC-Anlagen (Post-Combustion Capture) in fossil befeuerten Kraftwerken beispielsweise setzen Lösungsmittel auf Aminbasis wie Monoethanolamin ein, um CO2 aus dem Abgas aufzunehmen. Die PCC-Anlage umfasst einen Absorptionsturm, in dem das Lösungsmittel das CO2 bindet, und einen Desorptionsturm, in dem das CO2 durch Wärme freigesetzt und gesammelt wird. Das Lösungsmittel wird anschließend zur Wiederverwendung aufbereitet.
Im Gegensatz zur prozessbasierten CO2-Abscheidung, bei der Kohlendioxid aus industriellen Abgasen isoliert wird, entzieht Direct Air Capture (DAC) der Umgebungsluft CO2. Dabei wird Luft angesaugt und durch ein flüssiges oder festes Absorptionsmedium geleitet. Um das abgeschiedene CO2 für Transport und Speicherung vorzubereiten, wird es mithilfe von Wärme- und Vakuumtechnologien freigesetzt.
Das ursprüngliche Konzept für CCS sah vor, CO2-Abscheidungsanlagen mit Kompressions-, Transport- und Speichersystemen direkt in einzelne Anlagen wie Kraftwerke zu integrieren und sie unmittelbar hinter den Emissionskontrollsystemen zu positionieren. Heute werden jedoch CCS-Netzwerke, sogenannte „Cluster“, bevorzugt. In diesen Clustern sind mehrere CO2-emittierende Standorte über ein gemeinsames Pipelinesystem verbunden. Dieses leitet das Kohlendioxid aus verschiedenen Quellen zu zentralen Anlagen, wo es getrennt, gereinigt und verflüssigt wird. Aufgrund der unterschiedlichen und potentiell korrosiven Verunreinigungen im CO2-Strom können hier molybdänlegierte, korrosionsbeständige Rohrleitungen und Anlagen unerlässlich sein. Durch die gemeinsame Nutzung der Infrastruktur senken CCS-Cluster die Ausrüstungskosten für einzelne CO2-Emittenten.
Fallstudie: Northern Lights Joint venture (JV)
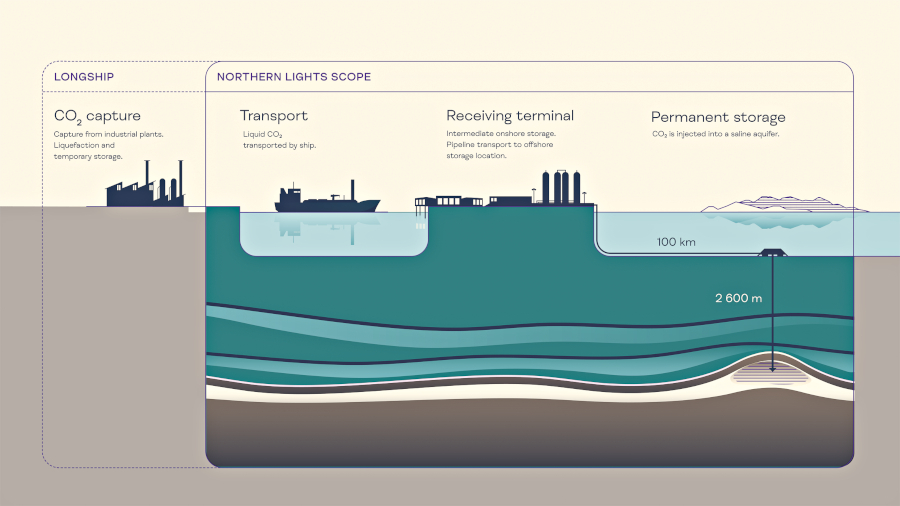
Northern Lights JV, eine Partnerschaft von Shell, Equinor und TotalEnergies, ist ein CCS-Projekt zur Sammlung, zum Transport und zur Speicherung von CO2 aus verschiedenen Quellen. Vier Schiffe mit einem Volumen von je 7.500 m3 transportieren verflüssigtes CO2 zu einem Empfangsterminal in Øygarden an der Westküste Norwegens. Die eingesetzte Transporttechnologie basiert auf Verfahren aus dem LNG-Transport, die für CO2 angepasst wurden.
Im Terminal, wo einige Anlagenteile aus Edelstahl Typ 316 bestehen, wird das CO2 zwischengelagert, bevor es über eine 110 km lange Offshore-Pipeline zu einem salzhaltigem Grundwasserleiter in 2.600 m Tiefe transportiert und dort sicher und dauerhaft gespeichert wird.
Am Injektionsstandort bestehen die unteren 200 m des Hüllrohrs und die Bohrlochrohre aus UNS S82551, einem Duplex-Edelstahl mit 1 Prozent Molybdän, und UNS S39274, einem 25Cr-Superduplex-Edelstahl mit 3 Prozent Molybdän.
Diese korrosionsbeständigen Legierungen sollen den aggressiven Bedingungen bei temporären Bohrlochabschaltungen standhalten und so die langfristige Integrität des Bohrlochs und den sicheren Einschluss von CO2 tief unter der Erde gewährleisten. Der Durchmesser der Rohre beträgt bis zu 25 cm.
Der Betrieb des Projekts startet 2025 mit einer Anfangskapazität von 1,5 Millionen Tonnen CO2 pro Jahr (Mtpa). In der ersten Phase werden 0,8 Mtpa CO2 aus einem Zementwerk in Brevik, Norwegen, und einem Müllheizkraftwerk in Oslo im Rahmen des staatlich geförderten Longship-Projekts eingelagert. Darüber hinaus hat Northern Lights kommerzielle Vereinbarungen zur Speicherung von 0,8 Mtpa aus der Ammoniakproduktion von Yara International in den Niederlanden sowie 0,43 Mtpa aus zwei Kraftwerken von Ørsted in Dänemark geschlossen.
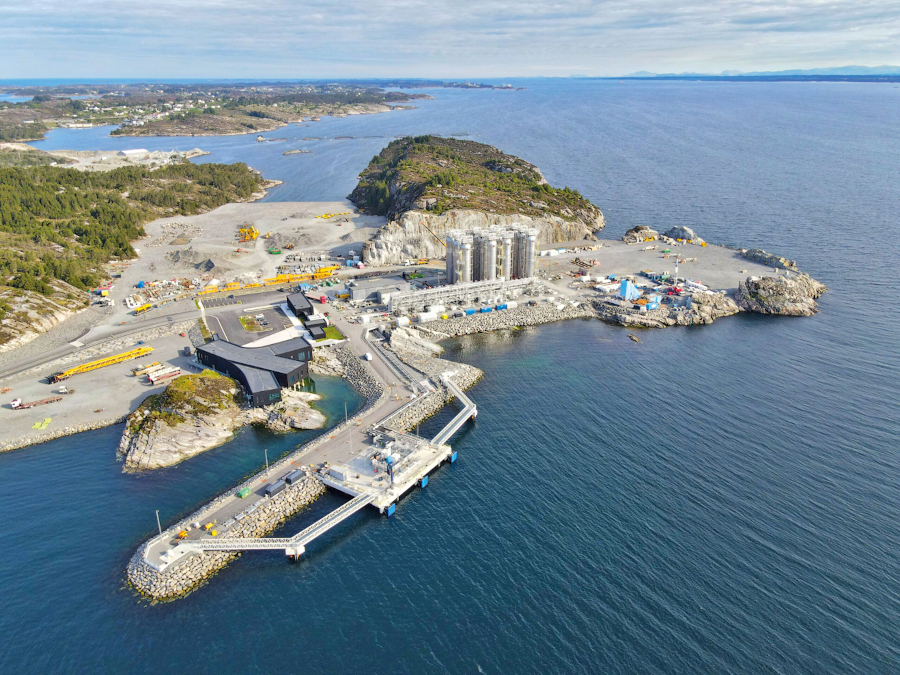
CO2-Nutzung
Die CO2-Abscheidung und -Nutzung (Carbon Capture and Utilization, CCU) ergänzt CCS indem das Kohlendioxid als Rohstoff für die Herstellung von Chemikalien, synthetischen Kraftstoffen und Polymeren wiederverwendet wird. Durch die Verwendung von abgeschiedenem CO2 anstelle von Kohlenwasserstoffen wie Erdgas oder Erdöl in der chemischen Synthese reduziert CCU die Notwendigkeit, zusätzliche neue fossile Ressourcen zu gewinnen und zu verarbeiten. Typische Anwendungen sind die Herstellung von Harnstoff, Salicylsäure und Polycarbonat.
Darüber hinaus kann CO2 zur Verbesserung der Betonherstellung beitragen, indem es zu Karbonat mineralisiert wird und so die mechanische Festigkeit des Materials erhöht. In der Getränkeindustrie findet CO2 breite Anwendung bei der Karbonisierung von Getränken.
Materialien und Komponenten für CCS und CCUS
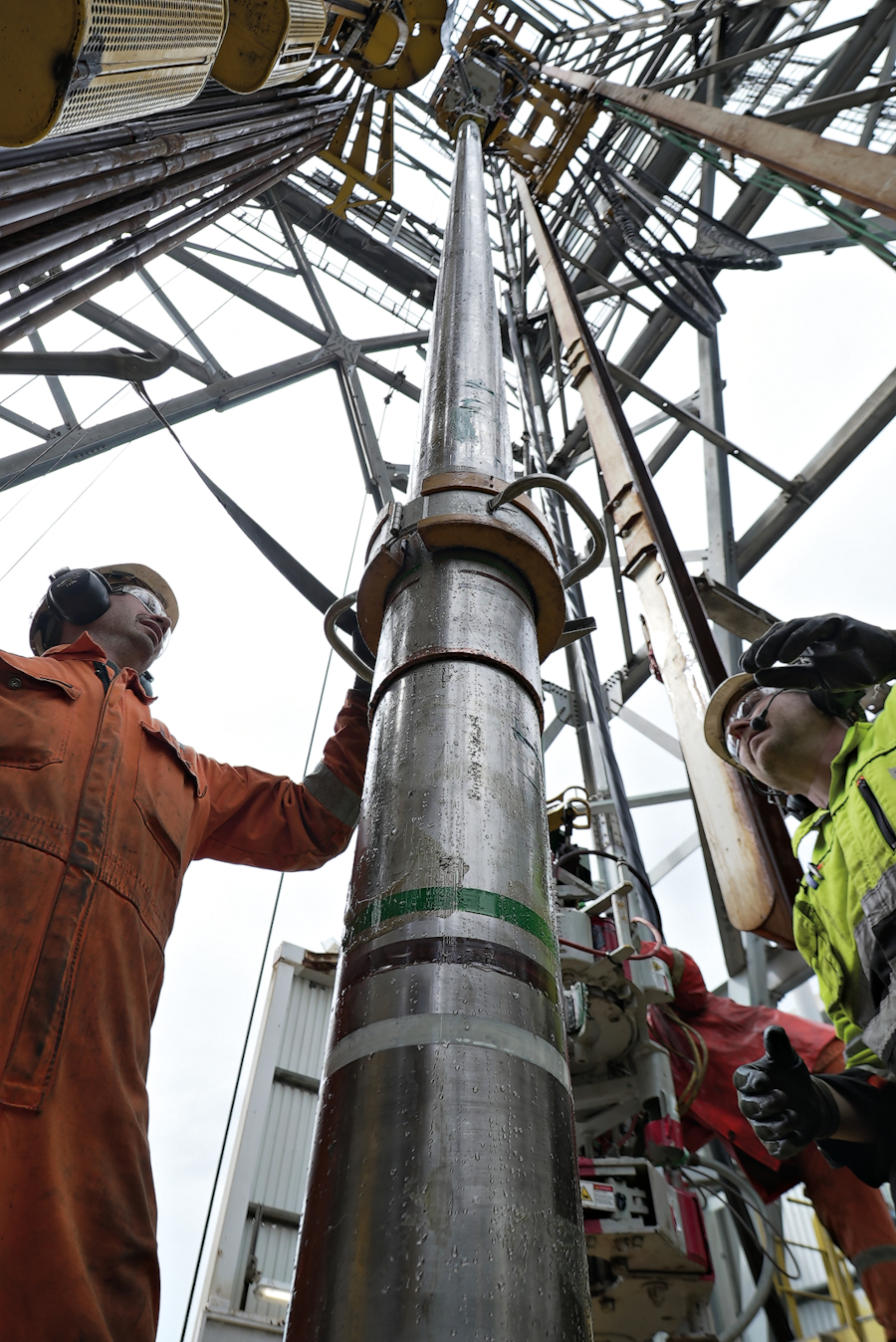
Neben Pipelines für CO2, die in der Regel aus unterpulvergeschweißten Kohlenstoffstählen bestehen, sind CCS- und CCUS-Anlagen auf eine Vielzahl bewährter Komponenten aus der Prozessindustrie angewiesen. Besonders im komprimierten oder verflüssigtem Zustand von CO2 sind Bauteile aus molybdänhaltigem Edelstahl unerlässlich, um Korrosionsprobleme zu vermeiden.
Nach dem „AMPP-Leitfaden 21532“ kann Edelstahl des Typs 316 für Kompressoren und Kühlvorrichtungen in Betracht gezogen werden, die der Verdichtung oder Verflüssigung von CO2 dienen. Der Leitfaden nennt Typ 316 zudem als Option für landseitige Rohrleitungen, die dichtes oder flüssiges CO2 bei Temperaturen bis zu -80°C transportieren. Für Offshore- oder küstennahe Leitungen, die einem höheren Chloridgehalt ausgesetzt sind, empfehlen sich Edelstähle mit 6 Prozent Molybdän oder beschichteter Typ 316-Edelstahl.
Auch andere wichtige Anlagenkomponenten wie Ventile, Durchflussmesser sowie Adsorptions- und Desorptionstürme erfordern korrosionsbeständige Werkstoffe. Für Bohrlochköpfe und Ventilbäume, die besonders durch Rückfluss von Wasser und saure Kondensate korrosionsgefährdet sind, eignet sich die Nickelbasislegierung Alloy 625 mit 9 Prozent Molybdän. Hüllrohre bestehen häufig aus niedriglegierten, oftmals molybdänhaltigen Stählen wie L80-Kohlenstoffstahl, F22 oder AISI 4130. Für Bohrlochrohre schließlich kann 25Cr-Superduplex-Edelstahl verwendet werden, der mit 3,5 Prozent Molybdän eine hervorragende Kombination aus Festigkeit und Korrosionsbeständigkeit bietet.
Stand der Industrie
Das Global CCS Institute berichtet von einem rasanten Wachstum der weltweiten CCS-Projekte. Bis Mitte 2024 befanden sich 628 Anlagen in Planung – ein Anstieg um 60 Prozent im Vergleich zum Vorjahr. Diese Projekte stehen für eine kumulative CO2-Abscheidekapazität von 416 Mtpa, was einem durchschnittlichen jährlichen Wachstum von 32 Prozent über sieben Jahre entspricht.
Von den derzeit 50 betriebenen Anlagen entfällt der größte Anteil auf die USA mit 19 Projekten, gefolgt von China mit 14, Kanada mit sieben sowie Norwegen und Island mit jeweils zwei Projekten. Australien, Brasilien, Ungarn, Katar, Saudi-Arabien und die Vereinigten Arabischen Emirate betreiben jeweils eine Anlage. In Europa hat sich die Zahl der in Planung befindlichen CCS-Anlagen im letzten Jahr auf 77 verdoppelt, was die zunehmende Verbreitung von CCS-Technologien in den Industrieländern verdeutlicht.
Auch wenn die vollständige Vermeidung von CO2-Emissionen das langfristige Ziel bleibt, gibt es Branchen, in denen Emissionen aktuell unvermeidbar sind. Hier bietet CCUS einen entscheidenden Lösungsansatz, um CO2 abzuscheiden, sicher unterirdisch zu speichern oder sinnvoll zu nutzen. Der Erfolg dieser Transformation hängt von einer zuverlässigen und widerstandsfähigen Infrastruktur ab – ein Bereich, in dem Molybdän eine zentrale Rolle für Beständigkeit und Langlebigkeit spielt.
Über den Artikel der Woche
Jede Woche beleuchten wir im Artikel der Woche ein spannendes Thema für die Edelstahlbranche. Weitere Artikel finden Sie auch in unserer Zeitschrift Edelstahl Aktuell. Um diese und viele weitere Artikel (fast) monatlich zu lesen, abonnieren Sie unsere Zeitschrift (erhältlich in Print und digital).
Möchten Sie als Autor mitwirken? Bitte kontaktieren Sie Sonja Wingels.
Jede Woche teilen wir einen neuen Artikel mit unserer Edelstahl Community. Machen Sie mit und lassen Sie uns Ihren Artikel auf Edelstahl Aktuell online und in gedruckter Form veröffentlichen.