Fotos: Oxford Flow
Das britische Unternehmen Oxford Flow hat ein Ventil entwickelt, dass flüchtige Methanemissionen gänzlich eliminieren und gleichzeitig die Ventilsicherheit erheblich verbessern soll. Der Klimaschutz und damit auch die Reduzierung der Methanemissionen stehen auf der Weltagenda. Bis November 2021 haben sich fast 90 Länder dem Global Methane Pledge verpflichtet, einer Initiative zur Reduzierung der weltweiten Methanemissionen bis 2030 um mindestens 30 Prozent gegenüber dem Niveau von 2020. US-Präsident Joe Biden verpflichtete sich auf der UN-Klimakonferenz in Glasgow 2021 für die USA zu dem Ziel, die Methanemissionen um etwa 50 Prozent unter das Niveau von 2005 zu senken.
Ein Beitrag von Dr. Chris Kennell, Oxford Flow.
Eine große Quelle industrieller Methanemissionen ist die Öl- und Gasindustrie. Methanemissionen, die bei der Förderung und dem Transport freigesetzt werden, geraten immer stärker in den Fokus der Öffentlichkeit.
Die Betreiber müssen dringend Maßnahmen umsetzen, um flüchtige Emissionen wirksam, zuverlässig und so schnell wie möglich zu beseitigen. Unzureichend überwachte und kontrollierte flüchtige Methanemissionen machen jährlich einen erheblichen Teil der Treibhausgasemissionen aus. Für 2019 schätzt die Internationale Energieagentur, dass 82 Millionen Tonnen Methanemissionen aus Öl- und Gasaktivitäten stammen – das entspricht fast einem Viertel aller anthropogenen Quellen. Trotz des erheblichen Treibhauspotenzials von Methan war die treibende Kraft bei der Bekämpfung flüchtiger Methanemissionen bis vor kurzem eher die Sicherheit als der Klimaschutz. Durch unter anderem strengere Gesetzgebungen wird sich auch hier der Blickwinkel ändern. Die Betreiber von vor- und nachgelagerten Anlagen werden zunehmend in den Blickpunkt rücken, wenn es darum geht, flüchtige Emissionen zu bekämpfen, um ein gutes Klimamanagement im Einklang mit den Erwartungen der Interessengruppen zu erreichen.

Hauptquelle für Lecks
Es gibt zwar viele Bereiche des Produktionsprozesses, die zu flüchtigen Emissionen führen, wie z. B. das Abfackeln, die Unversehrtheit von Bohrlöchern und ihrer Stilllegung, aber die Intaktheit der Durchflusskontrollinfrastruktur (auch Ventile genannt) ist eine wichtige Quelle für Leckagen und flüchtige Emissionen, die oft übersehen wird. Eine einzige große Verarbeitungsanlage – sei es eine Rohölraffinerie oder eine schwimmende Produktions- und Lagereinheit (Floating Production Storage and Offloading, kurz FPSO)- kann zwischen acht- und zehntausend Ventile aufweisen. Das kulminierende Potenzial dieser Ventilpopulationen, die für große Mengen flüchtiger Emissionen verantwortlich sind, sollte nicht unterschätzt werden.
Angesichts der Notwendigkeit, das Risiko einer Schwefelwasserstoffvergiftung und einer Explosion zu minimieren, werden von den Betreibern für die Inspektion der Dichtungsintegrität und für vorbeugende Wartungspläne jährlich hohe Beträge verwendet. Betrachtet man im Vergleich dazu die Ausgaben für die Vermeidung von flüchtigen Emissionen, so kann man zu dem Schluss kommen, es handelt es sich um den berühmten Tropfen auf dem heißen Stein. Die eigentliche Ursache des Problems flüchtiger Emissionen – die Ventilkonstruktion an sich – wird häufig nicht angegangen.
Bis vor kurzem hat die Ventilindustrie sich wiederholende Konstruktionsverbesserungen ohne größere Änderungen an der klassischen Ventilbauweise vorgenommen. Da die häufigsten Fehlerstellen der meisten Ventile jedoch die Spindel und der Stellantrieb sind, bleiben die Betreiber in einem Kreislauf gefangen, in dem sie Millionen für die Wartung ausgeben müssen, um Lecks zu finden, nachdem sie bereits das Sicherheitsrisiko erhöht oder die Umwelt beeinträchtigt haben.
Ein Team von Luft- und Raumfahrtingenieuren hat das Problem nun aus einem anderen Blickwinkel betrachtet und ein radikal neues Design entwickelt, das flüchtige Emissionen gänzlich eliminieren und gleichzeitig die Ventilsicherheit erheblich verbessern konnte.
Innovation durch Düsentriebwerk
Thomas Povey, Professor an der Universität Oxford, war nicht in der Lage, ein Druckregelventil zu finden, das den Anforderungen seiner Triebwerksforschung entsprach. Daher entwickelte er ein eigenes Ventil. Anstelle einer branchenüblichen flexiblen Membran entwarf Povey ein Ventil, das einen in das Ventilgehäuse integrierten Hydraulikkolben zur Betätigung verwendet. Das war genau das, was er für seine Forschung brauchte. Gleichzeitig aber erzielte das Design auch enorme Verbesserungen bei Leistung und Zuverlässigkeit gegenüber den Maßstäben der Ventilindustrie.
Das Geheimnis des Erfolgs lag in seiner Einfachheit. Durch den Wegfall der Membran und der zugehörigen Elastomere konnte Povey die Probleme der Ermüdung, Erosion und Versprödung deutlich verringern und somit die Achillesferse der Druckregelventile beseitigen. Aus dieser Idee heraus wurde 2015 das Unternehmen Oxford Flow gegründet, um die Technologie für eine breitere Anwendung zu vermarkten. Aufbauend auf Poveys Ansatz entwickelte Oxford Flow 2018 das ES-Ventil, bei dem die Spindel – die Hauptursache für flüchtige Emissionen -, der Stellantrieb und der Antriebsstrang entfernt wurden.
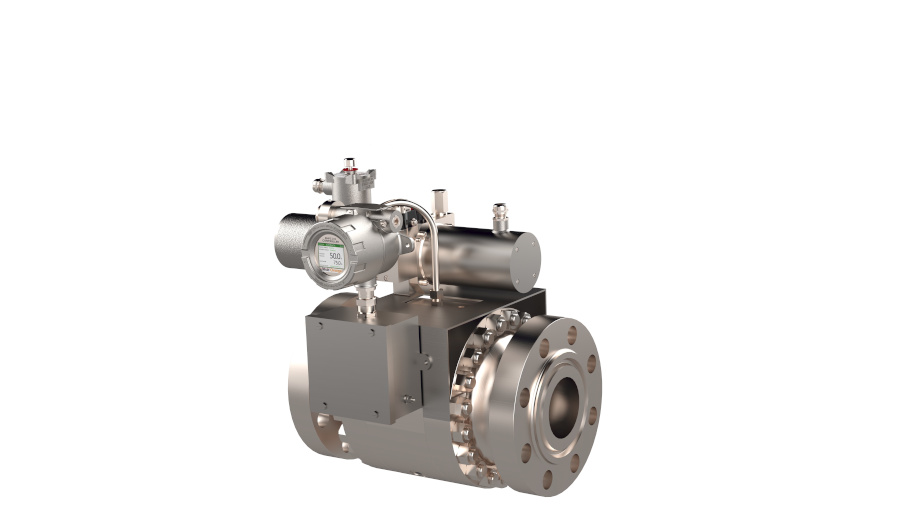
ES Ventil aus Edelstahl 316 von Oxford Flow
Das ES-Ventil aus Edelstahl 316 ist nach der Norm ISO 15848-1 Klasse A zertifiziert. Damit bietet es laut Oxford Flow eine Garantie für die Reduzierung und Beseitigung von Leckagen im Vergleich zur branchenüblichen Standardzertifizierung der Klasse B.
Für den Betrieb und die Instandhaltung ist das Design ein Wendepunkt, insbesondere für Betriebe mit einem hohen Anteil an kritischen Regelventilen oder für Betreiber mit alternden Anlagen. Betreiber, die damit beginnen, herkömmliche Ventile durch das neu konzipierte ES-Ventil zu ersetzen, müssen keine Ressourcen mehr für die Suche nach flüchtigen Emissionen bei diesem Teil ihres Ventilbestands bereitstellen. Auch müssen sie nicht mehr das gleiche intensive Wartungsprogramm einhalten, da Ausfälle im Zusammenhang mit dem Antriebsstrang ausgeschlossen sind und keine Spindelumfüllung mehr erforderlich ist. Als Ergebnis können die Betreiber eine Senkung der Betriebskosten um 20-30 % sowie eine Verdoppelung der mechanischen Lebensdauer des Ventils erwarten.
Dr. Chris Kennell ist seit 2018 Technical Sales Manager für betätigte Ventile bei Oxford Flow. Er hat im gesamten Unternehmen sowohl in der Technik als auch in der Geschäftsentwicklung gearbeitet. Zuvor war er Principal Engineer und leitete die Entwicklung der spindellosen ES-Ventiltechnologie von Oxford Flow. Kennell hat einen Master in Ingenieurwissenschaften von der University of Oxford und einen Doktortitel in Luft- und Raumfahrttechnik von der University of New South Wales, wo er über Hyperschall-Aerodynamik geforscht hat.
Über den Artikel der Woche
Jede Woche beleuchten wir im Artikel der Woche ein spannendes Thema für die Edelstahlbranche. Weitere Artikel finden Sie auch in unserer Zeitschrift Edelstahl Aktuell. Um diese und viele weitere Artikel (fast) monatlich zu lesen, abonnieren Sie unsere Zeitschrift (erhältlich in Print und digital).
Möchten Sie als Autor mitwirken? Bitte kontaktieren Sie Catrin Senger.
Jede Woche teilen wir einen neuen Artikel mit unserer Edelstahl Community. Machen Sie mit und lassen Sie uns Ihren Artikel auf Edelstahl Aktuell online und in gedruckter Form veröffentlichen.
Alle Bilder wurden vor der COVID-19-Pandemie bzw. unter Einhaltung der Abstandsregeln aufgenommen.