Fotos: VAU Thermotech GmbH & Co. KG
Seit 2008 ist VAU Thermotech GmbH & Co. KG erfolgreicher Hersteller von gelöteten, vollverschweißten und geschraubten Plattenwärmetauschern. Doch die Unternehmenshistorie reicht bis Ende der 1960er Jahre zurück. Mit einem Spaltgaskühler fiel der Startschuss für den Hybrid Tubular Plattenwärmetauscher. Welches Verdienst dabei Gamal El Din Nasser zukommt, wohin die Reise des Spaltgaskühlers führte und warum ein Winkelschleifer ein hervorragendes Werkzeug ist, beschreibt dieser Artikel.
50 Tage Arbeit erledigt in 60 Minuten
In den 1990ern war Osama Nasser als leitender Angestellter eines Herstellers für Wärmeübertrager damit beauftragt, die fünfte Stufe einer Verdampfungsstation in einer Zuckerfabrik zu ertüchtigen. Die Verdampfung ist ein mehrstufiger und energieintensiver Prozess, bei dem dem aus den Zuckerrüben gewonnenen Dünnsaft möglichst schonend Wasser entzogen wird.

Vereinfacht gesagt, wird der Saft von oben in den Apparat eingebracht und läuft nach unten durch einen dampfbeheizten Wärmeübertrager. Durch die Erhitzung des Dünnsafts verdampft ein Teil des darin enthaltenen Wassers, wodurch die Zuckerkonzentration steigt. Der eingedickte Saft wird an der Behälterunterseite aufgefangen und der nächsten Verdampfungsstufe zugeführt. Das Ziel ist eine Aufkonzentrierung des Safts auf einen Zuckergehalt von 60 bis 70 Prozent. Dazu werden im Durchschnitt sechs Verdampfungsstufen benötigt, wobei der Brüden der vorhergehenden Stufe zur Beheizung der nachfolgenden eingesetzt wird. Um Energie zu sparen, werden moderne Plattenfallfilmverdampfer verwendet, die sich durch geringe Temperaturdifferenzen zwischen der Saft- und Dampfseite auszeichnen.
Die Zuckerfabrik wollte einen in die Jahre gekommenen Verdampfer durch eine effizientere Lösung ersetzen. Dabei sollten sowohl die bestehende Rohrleitungsinfrastruktur möglichst wenig verändert und der vorhandene Apparatebehälter wiederverwendet werden. Basierend auf diesen Anforderungen und aufgrund der Leistung entschied sich der Auftraggeber für einen vollverschweißten Hybrid Tubular Plattenfallfilmverdampfer.
Um ein Anbrennen des Dicksaftes und damit die Bildung von Zuckerkohle, die den Apparat verstopfen und lahmlegen könnte, zu verhindern, muss der Flüssigkeitsfilm ohne abzureißen, in einer definierten Filmdicke und innerhalb eines genau festgelegten Temperaturintervalls durch den Prozess bzw. den Apparat geführt werden. Das Saftverteilungssystem an der Verdampferoberseite spielt daher eine entscheidende Rolle für den reibungslosen Betrieb des Verdampfers. Deswegen wurde es sorgfältig von Wissenschaftlern berechnet und von Ingenieuren designt: Es bestand aus einem Einlassrohr, das ein rundes Verteilungsblech mit 52 Reihen à 99 Löchern zu je 2 mm mit Dünnsaft berieselte.
Nach Beendigung der Montagearbeiten erfolgte ein Funktionstest der ertüchtigten Verdampferstufe. Um 22 Uhr plötzlich eine unangenehme Überraschung: Der Zuckersaft staute sich auf dem Verteilungsblech und der Prozess kam zum Erliegen. Das lag an zwei Dingen: 1. kam der Saft bereits von der vierten Stufe und war daher sehr viskos, wodurch 2. der Dicksaft aufgrund der hohen Oberflächenspannung nicht mehr durch die 2 Millimeter großen Löcher im Verteilungsblech „passte“. Es zeigte sich, dass theoretische Berechnungen nicht immer erfolgreich in die Praxis umgesetzt werden können.
Mitten in der Zuckerkampagne stand plötzlich die gesamte Fabrik still und es musste schnellstens eine Lösung gefunden werden. Anfangs war geplant, den Querschnitt aller 5.148 Löcher (99 Löcher à 52 Reihen) im Verteilungsblech zu erhöhen. Für das Aufbohren wurden pro Loch eine bis fünf Minuten veranschlagt, was einer Arbeitszeit von zehn und 50 Tagen entsprochen hätte.
Nach weiteren Beratungen bat Osama Nasser um einen Winkelschleifer, was alle Anwesenden sehr irritierte. Unter seiner Anleitung flexte ein Kraftwerksmitarbeiter mehrere 5 Millimeter lange Schlitze in das Lochblech, wodurch immer drei Löcher miteinander verbunden wurden. Dazwischen blieb ein schmaler Steg stehen, um die notwendige Stabilität des Blechs zu gewährleisten.
Nach etwa einer Stunde waren die Arbeiten abgeschlossen, der erneute Testlauf verlief reibungslos und die Fabrik konnte weiterarbeiten. In den folgenden Jahren verrichtete das improvisierte Saftverteilungssystem zuverlässig seinen Dienst. Das erfolgreiche Design wurde ab diesem Zeitpunkt Standard für alle nachfolgenden Saftverteilungssysteme.
Warum der Hybrid „Hybrid“ heißt
Ein Hybrid besteht aus Gehäuse und Heizfläche. Zum Gehäuse gehören Druckhalteplatten, Zuganker und Hauben, die ihrerseits aus Grundmaterial und angeschweißten Stutzen bestehen.
Die Heizfläche setzt sich aus Hüllrohren und mindestens einem Plattenpaket zusammen. Mehrere Plattenpakete ergeben einen Block.
Basis des Plattenpakets sind speziell geprägte Edelstahlformblechelemente, die auf- und aneinandergelegt und durch eine Rollnaht druckdicht verschweißt werden. Zwischen den Elementen ergeben sich ein rohr- und ein wellenförmiger Querschnitt bzw. eine Rohr- und eine Wellenseite. Die wellenförmige Struktur auf der Wellenseite versetzt das Medium in Turbulenzen, wodurch sich gute Wärmeübertragungsverhältnisse und eine geringe Verschmutzungsneigung ergeben. Das Plattenpaket selbst entsteht durch das Stapeln mehrerer Elemente, die an den Stirnseiten wiederum mit Quernähten verschweißt werden.


Die Elemente sind modular und variabel in Länge, Breite und Höhe aufbaubar. Dadurch lassen sich Wärmeübertragungsflächen zwischen 50 und 10.000 m² umsetzen und der Apparat kann anhand der bestehenden baulichen Gegebenheiten (Raumgröße, Rohrleitungen, Anschlüsse) gebaut werden.
Basierend auf Auslegungsparametern und gewünschten thermodynamischen Eigenschaften der Wärmeübertragerelemente werden die Strömungsquerschnitte des Hybrid durch die flexibel einstellbare Prägetiefe des Prägewerkzeugs angepasst. Die Prägetiefe hat direkten Einfluss auf die Druckverluste, den Wärmeübergang und die Geometrie der Wärmeübertragungsfläche. Möglich sind Durchmesser zwischen fünf und zehn Millimetern auf der Rohrseite und Spaltbreiten zwischen vier und acht Millimetern auf der Wellenseite.
Da der Hybrid Tubular Plattenwärmetauscher aufgrund seines speziellen Designs einerseits eine Rohrseite ähnlich wie ein Rohrbündelwärmeübertrager (RWÜ) besitzt, andererseits aus Platten aufgebaut ist, wurde der Zwitter „Hybrid“ genannt. Um die Verwandtschaft mit dem RWÜ hervorzuheben, wurde das Wort „Tubular“ hinzugefügt.
Die wandelbare Welt des Edelstahls
Die Anwendungsbereiche des Hybrids sind genauso flexibel wie sein Design – es kommt nur auf die Wahl des entsprechenden Edelstahls für die Plattenpakete an.
Vor Kurzem wurde ein bayerisches Heizkraftwerk mit Kraft-Wärme-Kopplung einer Ertüchtigung unterzogen. Eingesetzt wurden zwei Heizkondensatoren von VAU Thermotech mit jeweils einem Hybrid Tubular Plattenwärmeübertrager. Zum Erhitzen des im Kreuzstrom geführten Wassers für die Fernwärme wird ausgekoppelter Turbinen-Dampf verwendet. Aufgrund der Wasserqualität im Fernwärmenetz fiel die Entscheidung auf Plattenpakete aus 1.4404er Edelstahl. Mit den neuen Heizkondensatoren konnte die Heizleistung von 32 MW auf 48 MW gesteigert und aufgrundder flexiblen Bauweise des Hybrids der vorhandene Platz im Kesselhaus exakt so wiederverwendet werden. Lediglich die Rohrleitungen mussten leicht modifiziert werden.

Aber nicht nur Standardedelstähle finden Verwendung für die Hybrid-Plattenpakete: Ein Unternehmen für Spezialchemie ließ sich beispielsweise für seine Ethylbenzol-Anlage zwei Wärmeübertrager mit einer Leistung von je 1.235 kW auf Basis des Hybrid bauen. Im Kreuzstrom wurden darin das zu erwärmende Gas und Heizdampf geführt. Da beim Prozess Temperaturen von 650 °C bzw. 800 °C auftraten, mussten die Plattenpakete aus 1.4958er Edelstahl gefertigt werden, da dieser eine hohe Zeitstandfestigkeit bei hohen Temperaturen gewährleistet.
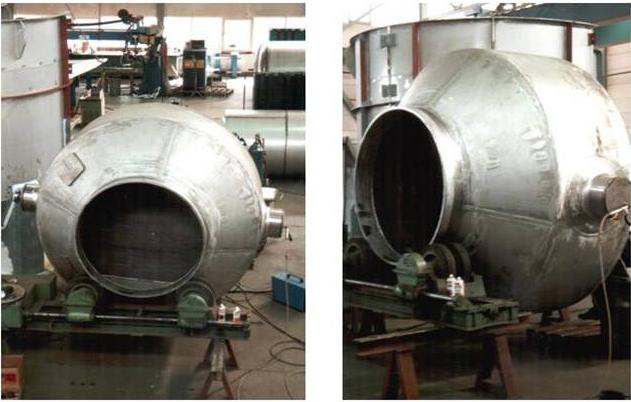
Ein Hersteller von Laboreinrichtungen aus Süddeutschland ließ einen Reinstdampferzeuger mit 200 kW Leistung auf Basis eines Hybrid Tubular Plattenwärmeübertragers fertigen. Auf 15 m² Heizfläche werden im Apparat Heizdampf unter Vakuum bei 250 °C und Reinstwasser bei 250 °C und 8 bar Druck im Kreuzstrom geführt. Werkstoff für den Bau der Plattenpakete war 1.4539.
Plattenpakete aus 1.4547 / SMO 254 kamen in einem Nitrit-Heizer mit einer Leistung von 2.750 kW zum Einsatz. Im Apparat wurde als Heizmedium Dampf im Kreuzstrom zur Nitritlösung geführt. Gebaut wurde dieser Apparat für ein Spezialchemieunternehmen aus Deutschland.
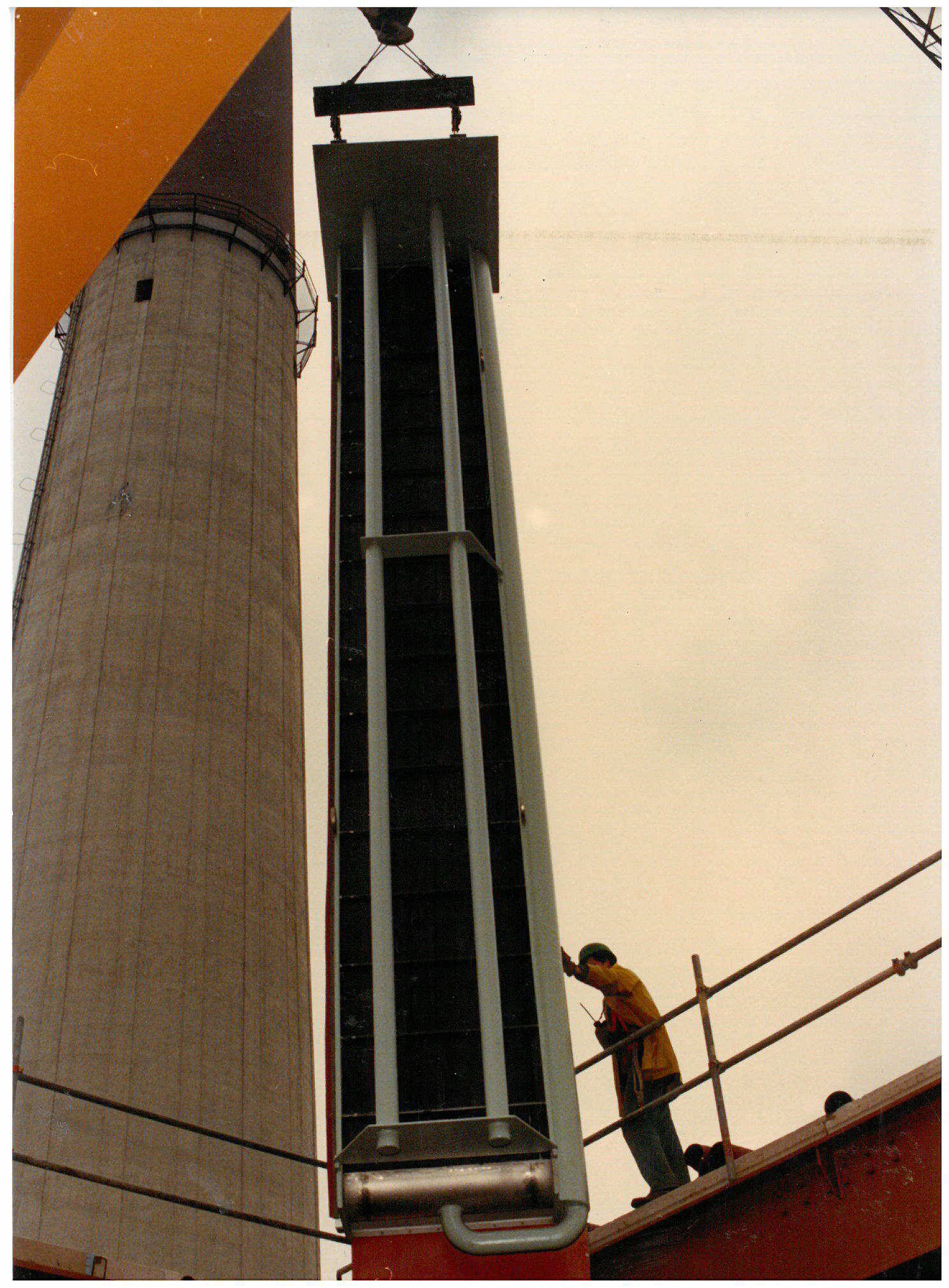
Korrosionsbeständigkeit stand für ein deutsches Chemiewerk im Fokus. Daher wurde der Luftkühler mit einer Leistung von 1.451 KW und einer Heizfläche von 145 m² aus 2.4360er Edelstahl gebaut. Im Plat-tenpaket werden Wasser und Luft im Kreuzstrom aneinander vorbeigeführt.
Auch international sind Apparate mit Hybrid Tubular Plattenwärmetauschern gefragt. Ein US-amerikanischer Produzent von Wasserverteilungssystemen orderte gleich mehrere Apparate. Für die Plattenpakete wurde zum einen Inconel 600 verwendet, da in einem Apparat Flusswasser bzw. das Kältemittel R134a (Tetrafluorethan) in voneinander getrennten Kreisläufen geführt werden. Bei einem anderen Apparat wurden Wasser und Chlorwasserstoff geführt und daher Hastelloy C 276 für die Edel-stahlplatten des Wärmetauschers verwendet.
Hastelloy C 276 war auch der Werkstoff der Wahl für mehrere Produktkühler eines ungarischen Chemieunternehmens. Eingesetzt wird als Kühlmittel Wasser, das entweder Aniliniumchlorid oder andere Reaktionsgemische auf die gewünschte Temperatur bringt. Die Prozesstemperaturen liegen je Apparat entweder bei 60 oder 150 °C die Heizleistungen zwischen 266 und 800 kW.
Hastelloy in der Legierung C4 wurde für die Hybrid Plattenpakete eines Starkwasserkühlers mit einer Heizfläche von 32 m² und einer Leistung von 700 kW eingesetzt. Der Apparat wird von einem deutschen Stahlhersteller verwendet.
Flexibel bleiben: vom Spaltgaskühler zum Hybrid Tubular Plattenwärmetauscher
Ursprünglich wurde der Hybrid Tubular Plattenwärmetauscher als Spaltgaskühler für Luftzerlegungsanlagen von Gamal El Din Nasser, dem Vater von Osama Nasser, Ende der 1960er Jahre erfunden und 1968 patentiert. Da der Apparat für diese Aufgabe nur eingeschränkt geeignet war, kaufte Gamal El Din Nasser das Patent zu einem symbolischen Preis zurück und machte sich mit Osama Nasser 1981 selbstständig.
Bis Gamal El Din Nasser im Jahr 1989 in den Ruhestand ging, wurde der Plattenwärmeübertrager unter den Namen „BAVEX®“ bzw. „IPEX®“ z.B. als Verdampfer oder Vorwärmer in der chemischen oder der Lebensmittelindustrie vermarktet. Zum Einsatz kamen diese auch in Meer- und Brackwasserentsalzungsanlagen bzw. bei der Wärmerückgewinnung in Entschwefelungs- und Rauchgasentstickungsanlagen. 1987 folgte die Premiere in der Zuckerindustrie.
Nach dem Ausscheiden Gamal El Din Nassers aus dem Berufsleben, war Osama Nasser zwischen den Jahren 1990 und 2008 als leitender Angestellter bzw. Geschäftsführer bei großen Wärmeübertragerherstellern tätig. Dort trieb er die Entwicklung des Hybrids weiter voran und vermarktete diesen ab 1992 erfolgreich als Platten-Fallfilmverdampfer in der Zuckerindustrie. 1997 wurde erstmalig eine komplette fünfstufige Verdampferstation in einer österreichischen Zuckerfabrik ausgerüstet, 1998 folgten Zuckerfabriken in den USA und Belgien.
Mit der Übernahme der Münchner VAU Werkzeug- und Gerätebau GmbH im Jahr 2008 machte sich Osama Nasser erneut selbstständig, um die vollverschweißten Plattenwärmeübertrager selbst herzustellen und zu verkaufen. 2009 firmierte das Unternehmen in VAU Thermotech GmbH & Co. KG um und das Portfolio wurde um gelötete und geschraubte Plattenwärmetauscher ergänzt.
2014 erfolgte während des laufenden Geschäftsbetriebs der Umzug ins thüringische Heldrungen, dem heutigen Stammsitz des Unternehmens. Gleichzeitig wurden das Know-how und die Produktionskapazitäten des französischen Klimatechnik-Anlagenbauers CIAT übernommen, um Plattenwärmetauscher für die Kältetechnik zu produzieren.
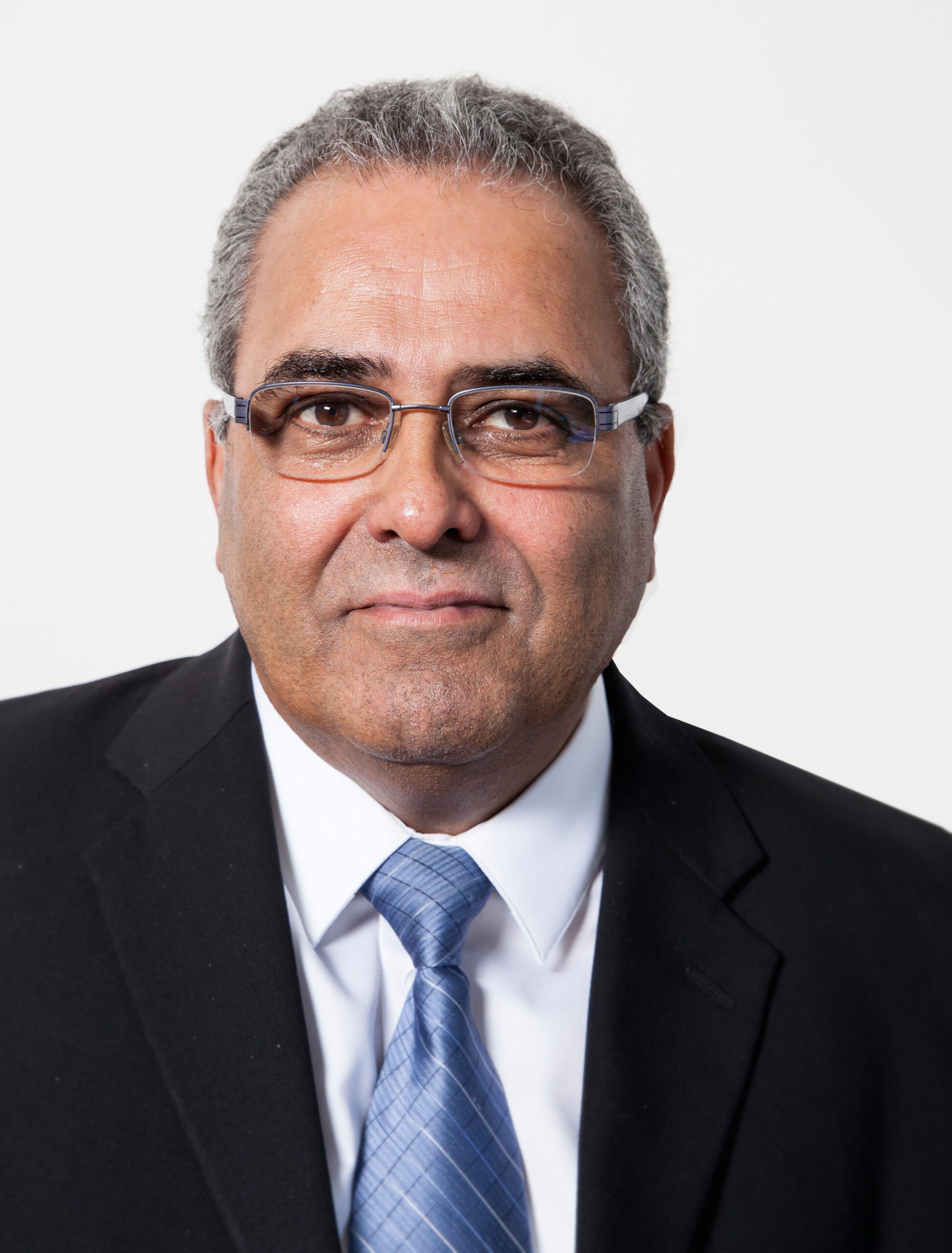
Im Jahr 2022 erfolgte die Markteinführung eines weiteren vollverschweißten Hybrid Tubular Plattenwärmeübertragers – dem VAU COMPEX. Nach längerer Forschungs- und Entwicklungszeit war es schließlich gelungen, die Fertigung insoweit zu standardisieren, dass dieser Hybrid für bestimmte Anwendungsszenarien, wie z.B. Kälteanlagen, „von der Stange“ lieferbar ist. Das spart Kosten und verkürzt die Lieferzeit.
Doch auch wenn Wärmeübertrager an sich schon ziemlich optimal sind, sind es die Feinheiten, die den Unterschied machen. Daher produziert VAU schon immer in Deutschland und setzt seit jeher auf Edelstahl-Zulieferer aus Deutschland und Europa. Das hält die Lieferketten kurz, macht sie ausfallsicher und ermöglicht es letztendlich, gelötete Standard-Plattenwärmetauscher innerhalb von 24 Stunden versandbereit zu haben. Und dank der ISO 9001:2015 Zertifizierung garantiert das Unternehmen eine gleichbleibend hohe Qualität.
Über den Artikel der Woche
Jede Woche beleuchten wir im Artikel der Woche ein spannendes Thema für die Edelstahlbranche. Weitere Artikel finden Sie auch in unserer Zeitschrift Edelstahl Aktuell. Um diese und viele weitere Artikel (fast) monatlich zu lesen, abonnieren Sie unsere Zeitschrift (erhältlich in Print und digital).
Möchten Sie als Autor mitwirken? Bitte kontaktieren Sie Catrin Senger.
Jede Woche teilen wir einen neuen Artikel mit unserer Edelstahl Community. Machen Sie mit und lassen Sie uns Ihren Artikel auf Edelstahl Aktuell online und in gedruckter Form veröffentlichen.
Alle Bilder wurden vor der COVID-19-Pandemie bzw. unter Einhaltung der Abstandsregeln aufgenommen.