Schwelgern 1 gehört zu den modernsten Hochöfen der Welt mit einer potentiellen Leistung von 10.000 t pro Tag. An den Blasformen wurden im Laufe des Projekts 40 SIP-Boxen (grau-blau im Bild) installiert, welche starke, diskontinuierliche Impulse mit technischem Sauerstoff in das Koksbett injizieren, um eine bestmögliche Tiefenwirkung zu erzielen. | Foto: thyssenkrupp AT.PRO tec GmbH
Die thyssenkrupp AT.PRO tec GmbH ist bekannt für die Entwicklung des Sequenz-Impuls-Prozesses. Zur Anwendung gekommen an Kupolöfen konnte er deren Wirtschaftlichkeit in der Vergangenheit deutlich steigern. In über 10 Jahren Entwicklungsarbeit mit Schubert & Salzer Control Systems als Partner gelang es Dr. Rainer Klock und dem Team der AT.PRO tec, die SIP-Technologie mithilfe von Gleitschieberventilen auch an Hochöfen zum Einsatz zu bringen – im Ergebnis werden so bis zu 100 kg CO2 pro produzierter Tonne Roheisen eingespart.
Ein Fachbeitrag von Sandro Caravita, Schubert & Salzer Control Systems GmbH
Die Geschichte des Hochofenprozesses ist eine lange Geschichte großer Innovationen und technischer Verbesserungen. Immer wieder gab es mutige Innovatoren die bereit waren, gängige Verfahren in Frage zu stellen, um den Herstellungsprozess von Roheisen weiter zu optimieren. So schaffte es Abraham Darby z.B. im 18. Jahrhundert Koks anstelle von Holzkohle einzusetzen, wodurch die Hochöfen deutlich größer und effizienter wurden. Im 19. Jahrhundert gelang Edward Alfred Cowper ein Innovationssprung bei den neu aufkommenden Winderhitzern. Die sogenannten „Cowper“ sind heute Bestandteil jeder Hochofenanlage.
Mit dem „Sequenz-Impuls-Prozess mit induzierten Stoßwellen“ erreicht der Hochofen nun die nächste Stufe der Evolution. Hinter dem SIP-Verfahren stehen die thyssenkrupp AT.PRO tec GmbH und der heutige Geschäftsführer Dr. Rainer Klock. Als Team entwickelten sie die Technologie über einen Zeitraum von mehr als 10 Jahren so weiter, dass ihr Einsatz am Hochofen überhaupt erst möglich wurde. Die Mitarbeiter von AT.PRO tec bündeln heute hochspezialisiertes Expertenwissen aus Wissenschaft und Industrie zum Einsatz von Gasen in Schmelzprozessen.
Der zugrundeliegende Gedanke des neuen Verfahrens ist es, die tiefer im Ofeninneren gelegenen Bereiche zu aktivieren. Bei der derzeitigen Verfahrenstechnik blockieren nicht vollständig reagierte Feinpartikel das Koksbett, wodurch die Gasströmung und die Hitze nicht tief genug in den Ofen eindringen können. Es entsteht ein Kegel aus Koks, der sogenannte „Tote Mann“.
Die Lösung: Starke, diskontinuierliche Impulse ermöglichen die notwendige Tiefenwirkung des technischen Sauerstoffs. Das kurzzeitige, lokale Überangebot an Sauerstoff ermöglicht eine vollständigere chemische Umsetzung der Feinpartikel – auch tief im Koksbett. Die mit den Impulsen einhergehenden Stoßwellen brechen Verkrustungen an dieser Stelle auf und vermischen den Inhalt durch starke Turbulenzen. Sie sorgen dadurch für eine gleichmäßigere Durchgasung und einen besseren Abfluss des flüssigen Metalls und der Schlacke.
Phase 1: ASIPGO – Das Verbund-Forschungsprojekt von thyssenkrupp und der RWTH Aachen (2007-2011)
Im kleineren Maßstab, an Kupolöfen, funktioniert die Technologie schon seit Jahren erfolgreich und ermöglicht eine deutliche Steigerung der Wirtschaftlichkeit. Der Einsatz an den erheblich größeren Hochöfen war jedoch noch vollkommen unerforscht.
Als AT.PRO tec sich damit an die RWTH Aachen und das dort situierte Institut für Eisenhüttenkunde (IEHK) wandte, hatte Rainer Klock soeben seine Diplomarbeit fertiggestellt. Für das neue Forschungsprojekt, welches durch thyssenkrupp als Industriepartner unterstützt wurde, suchte die RWTH einen wissenschaftlichen Mitarbeiter. „Das war für mich die perfekte Gelegenheit. Nicht nur konnte ich sofort im Anschluss an mein Diplom die Doktorarbeit schreiben, das Projekt bot auch die Möglichkeit direkt an einem der größten Hochöfen Europas zu arbeiten“, berichtet Dr. Klock später. „Das Projekt ASIPGO sollte über drei Jahre hinweg zwei Ziele verfolgen: erstens, den Einsatz des SIP-Verfahrens an Kupolöfen durch Automatisierung zu verbessern und zweitens den Einsatz des SIP-Verfahrens an Hochöfen zu ermöglichen.“
Rainer Klock fokussierte sich im Rahmen seiner Doktorarbeit auf die Forschung für den Einsatz am Hochofen. Dabei wurden zunächst die physikalischen und chemischen Prozesse untersucht, die dem SIP-Verfahren an Kupolöfen zum Erfolg verhalfen. Die Forschergruppe, bestehend aus Mitarbeitern von thyssenkrupp AT.PRO tec, thyssenkrupp Steel Europe und der RWTH Aachen, wollte die Prozesse in der Wirbelzone eines Hochofens und wie diese durch Sauerstoffimpulse wahrscheinlich beeinflusst würden, genau verstehen, um die Technologie mit dem gesammelten Wissen vom Kupolofen auf den Hochofen übertragen zu können.
Das Prinzip dieses Ventils ist faszinierend einfach: zwei aufeinander gleitende und gegeneinander dichtende Schlitzscheiben. Eine senkrecht zur Strömungsrichtung fixierte Dichtscheibe, auf der eine weitere, bewegliche Scheibe mit der gleichen Schlitzanordnung verschoben wird, wodurch sich der Durchflussquerschnitt verändert. Die anliegende Druckdifferenz presst die bewegliche Scheibe auf die feststehende Scheibe und trägt dadurch zur Dichtigkeit bei. Die durch dieses Prinzip erreichbaren, kurzen Öffnungszeiten und die Druckbeständigkeit bei großen Nennweiten waren letztendlich ausschlaggebend.
Auf Basis dieser Erkenntnisse am IEHK wurde schließlich eine SIP-Versuchsanlage für Hochöfen konstruiert. Im Vergleich zur SIP-Anlage für Kupolöfen arbeitete man nun mit deutlich größeren Nennweiten und Drücken. Die Anlage musste daher angepasst und mit geeigneten Komponenten ausgestattet werden. Ein Hauptaugenmerk lag dabei auf den sogenannten Pulsventilen. Diese mussten in der Lage sein, eine möglichst starke Stoßwelle zu erzeugen. Nach einer langen Untersuchungsreihe mit unterschiedlichen Ventiltypen konnte sich das Gleitschieberventil von Schubert & Salzer durchsetzen.
Phase 2: Vom Versuch zum großindustriellen Einsatz (2011 – 2020)
Die ersten Tests mit der SIP-Versuchsanlage am Hochofen Schwelgern 1 in Duisburg lieferten so vielversprechende Ergebnisse, dass thyssenkrupp Steel Europe sich entschloss, das Verfahren auch über das Forschungsprojekt hinaus weiterzuentwickeln. Mit seinen 13,6 m Gestelldurchmesser, einer Gesamthöhe von ca. 110 m und einem inneren Volumen von 4.416 m3 hat der Hochofen Schwelgern 1 eine potentielle Leistung von 10.000 t pro Tag. Die geschweißte Stahlkonstruktion, die im Inneren mit feuerfestem Material ausgekleidet ist und über einen geschlossenen Kühlwasserkreislauf verfügt, zählt zu den modernsten Hochöfen der Welt. Hier sollte Rainer Klock die Weiterentwicklung des SIP-Verfahrens als Betriebsingenieur leiten und wurde gen Sommer 2010 von thyssenkrupp Steel Europe unter Vertrag genommen.

Einerseits musste auf Basis der SIP-Versuchsanlage nun ein industriell einsatzfähiger Prototyp entstehen. Andererseits ging es darum, diesen Prototypen weiter für den Prozess zu optimieren. „Um die Wirkung unseres Verfahrens weiter zu verbessern, begannen wir, uns den Stoßwellen zu widmen, die mit jedem Impuls einhergingen.“, erklärt Dr. Rainer Klock, inzwischen promoviert zum Doktor der Metallurgie. „Wir waren überzeugt, dass sie als Teil des SIP-Verfahrens einen wichtigen Beitrag zu dessen positiver Wirkung auf den Prozess leisteten. Mit stärkeren Stoßwellen wollten wir die Wirbelzone vergrößern und Verkrustungen im Koksbett aufbrechen, dadurch die Permeabilität erhöhen und infolgedessen mit größeren Reaktionsoberflächen die Effizienz des Hochofenprozesses steigern.“
„Das Projektteam der AT.PRO tec setzte sich damals mit uns in Verbindung und erklärte uns, was sie vorhatten.“, erzählt Marcel Mokosch, Technischer Vertrieb bei Schubert & Salzer Control Systems. „Zur Erzeugung von Impulsen mit noch stärkeren Stoßwellen, mussten die hohen Öffnungsgeschwindigkeiten noch weiter optimiert werden, um extrem kurze Öffnungszeiten zu erreichen. Grundsätzlich waren Gleitschieberventile für diese Anwendung die perfekte Wahl. Der typische Hub zwischen „offen“ und „geschlossen“ beträgt nur ca. 8 mm. Dieser kurze Hub geht mit sehr geringen bewegten Massen einher. Deshalb werden auch nur geringe Antriebskräfte benötigt, wodurch das Ventil letztlich sogar kompakter ist als die meisten anderen Ventiltypen.“
Nach diesem Gespräch lief die erste „SIP-Box“, der Prototyp der neuen Anlage, für einen Zeitraum von vier bis fünf Jahren im Dauerbetrieb und wurde dabei permanent weiter optimiert. Schritt für Schritt ist das eingesetzte Gleitschieberventil dabei über Jahre hinweg mit der Anlage und dem Prozess gereift. In enger Zusammenarbeit wurden verschiedene konstruktive Änderungen vorgenommen und anschließend in der Praxis erprobt, um das Ventil an die Anforderungen der Anwendung anzupassen.
„Schließlich hatten wir es geschafft, das Ventil auf Rekord-Öffnungsgeschwindigkeiten von nur 2 ms hin zu optimieren. Dadurch war es möglich, Impulse, die tief in das Koksbett reichen, mit wirklich starken Stoßwellen freizusetzen“, führt Marcel Mokosch aus. „Die extremen Schaltgeschwindigkeiten bei gleichzeitig hohen Drücken und hoher Schalthäufigkeit brachten das Ventil nun aber an seine Belastungsgrenzen. Diese Kombination an Anforderungen war damals wirklich eine Herausforderung für uns. Wir sahen darin aber auch eine große Chance für die Gleitschiebertechnologie, sich zu beweisen. Um unter den extremen Betriebsbedingungen für den Betreiber akzeptable Ventilstandzeiten zu erreichen, mussten die mechanischen Grenzen des Ventils durch konstruktive Änderungen erweitert werden. Ein Jahr Standzeit, also mehrere Millionen Schaltungen, war das erklärte Ziel.“
2015 war es schließlich so weit: thyssenkrupp Steel Europe und thyssenkrupp AT.PRO tec GmbH begannen mit der Entwicklung, Errichtung und dem Betrieb einer vollständigen Sauerstoffimpulsanlage am Hochofen 1 in Duisburg-Schwelgern. In den kommenden Jahren wurde die Optimierung der SIP-Boxen finalisiert. Im laufenden Betrieb wurden an den 40 Blasformen des Hochofens SIP-Vorrichtungen installiert.
Erfolgreicher Projektabschluss
Im Herbst 2020 wurde die SIP-Anlage schließlich fertig gestellt. 40 SIP-Boxen warteten auf ihren Einsatz. Über einen Zeitraum von mehreren Wochen wurden die Boxen Schritt für Schritt aktiviert. Die Auswirkungen auf den Prozess wurden dabei mit Spannung beobachtet.
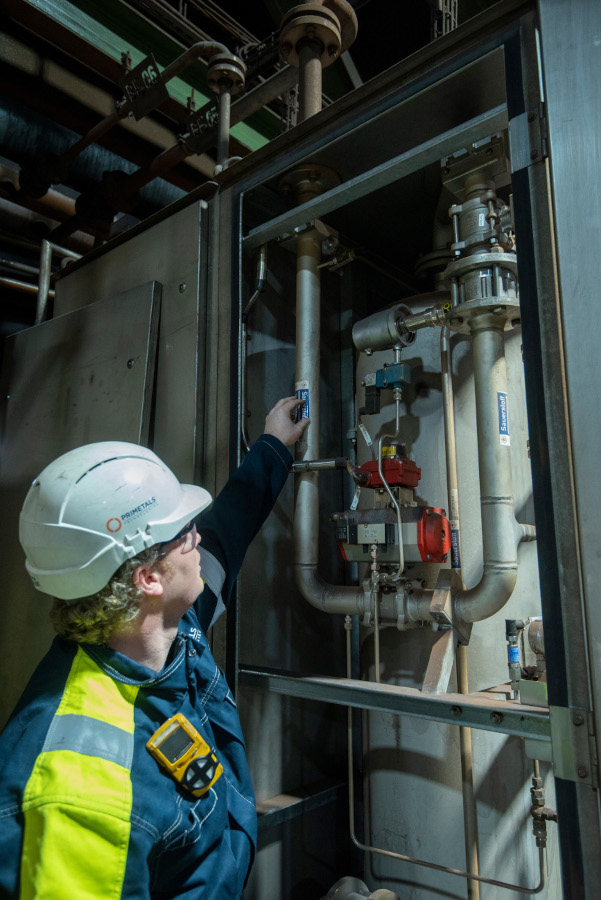
Das SIP-Verfahren hat sich am Hochofen Schwelgern 1 in weniger als 2 Betriebsjahren amortisiert und spart nun jährlich mehrere Millionen Euro an Kosten. Der Gesamtverbrauch an Reduktionsmitteln (Koks und Einblaskohle) konnte, durch die Effizienzsteigerung, signifikant gesenkt werden. Dies spiegeln auch die CO2-Einsparungen zwischen 50 und 100 kg pro produzierter Tonne Roheisen wider. Die jährlichen CO2-Einsparungen belaufen sich auf weit über 100.000 t.
Für thyssenkrupp AT.PRO tec ist das ganze Projekt ein großer Erfolg: „Nach einjährigem Dauerbetrieb hat sich gezeigt, dass die Gleitschieberventile den extremen Einsatzbedingungen unserer Anwendung hervorragend gewachsen sind. Die langjährige, gemeinsame Entwicklungsarbeit mit Schubert & Salzer hat sich mehr als gelohnt. Einen so ausdauernden und zuverlässigen Entwicklungspartner zu finden, ist keine Selbstverständlichkeit“, erklärt Dr. Rainer Klock, heute Geschäftsführer der thyssenkrupp AT.PRO tec GmbH. „Eines unserer Zukunftsprojekte ist es nun, mit Hilfe eines Level 2 Automatisierungssystems, die SIP-Technologie und den Hochofenprozess direkt zu verlinken, um weiterführende und automatisierte Prozessoptimierungen zu ermöglichen. Zunächst wird es aber unser Ziel sein, der SIP-Technologie zum weltweiten Erfolg zu verhelfen.“
Als die Technologie zum ersten Mal voll einsatzfähig war, entschied thyssenkrupp AT.PRO tec, dass die Partnerschaft mit einem der führenden Anbieter von Hochofenanlagen und -ausrüstungen hilfreich dabei wäre, dieses Ziel zu erreichen. Nach mehrmonatigen Verhandlungen wurde im August 2021 eine exklusive weltweite Marketing- und Vertriebsvereinbarung mit Primetals Technologies Ltd. unterzeichnet.
„Unser zuverlässiger Partner Primetals Technologies soll diese Technik weltweit vermarkten und auch anderen Stahlherstellern zugänglich machen“, schließt Dr. Rainer Klock.
Über den Artikel der Woche
Jede Woche beleuchten wir im Artikel der Woche ein spannendes Thema für die Edelstahlbranche. Weitere Artikel finden Sie auch in unserer Zeitschrift Edelstahl Aktuell. Um diese und viele weitere Artikel (fast) monatlich zu lesen, abonnieren Sie unsere Zeitschrift (erhältlich in Print und digital).
Möchten Sie als Autor mitwirken? Bitte kontaktieren Sie Catrin Senger.
Jede Woche teilen wir einen neuen Artikel mit unserer Edelstahl Community. Machen Sie mit und lassen Sie uns Ihren Artikel auf Edelstahl Aktuell online und in gedruckter Form veröffentlichen.